How Global Thermoforming is Staying Clean and Healthy During COVID-19
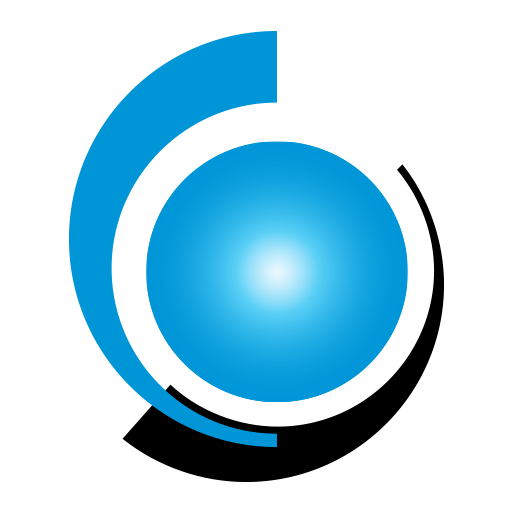
When the COVID-19 pandemic entered the news in March, Global Thermoforming saw both opportunities and challenges. With our existing capacities for quality thermoforming, close tolerance forming, and precision trimming at our Tempe, AZ, and Nashville, TN manufacturing facilities, we have already created a lot of innovative thermoforming for our medical industry clients. When the urgent need for Personal Protective Equipment (PPE) for healthcare providers was recognized, our skill with rapid prototyping and creating innovative designs prepared us to help right away. The opportunity to develop and supply essential medical components and protective equipment was one that we gladly accepted.
As we are supplying an essential service, our employees have continued to work throughout the Shelter-In-Home restrictions. We’ve always been proud of the way we keep our team safe and healthy. When the challenge of new procedures arrived with the coronavirus epidemic, we implemented new best practices and protocols, changing and improving our routines as needed.
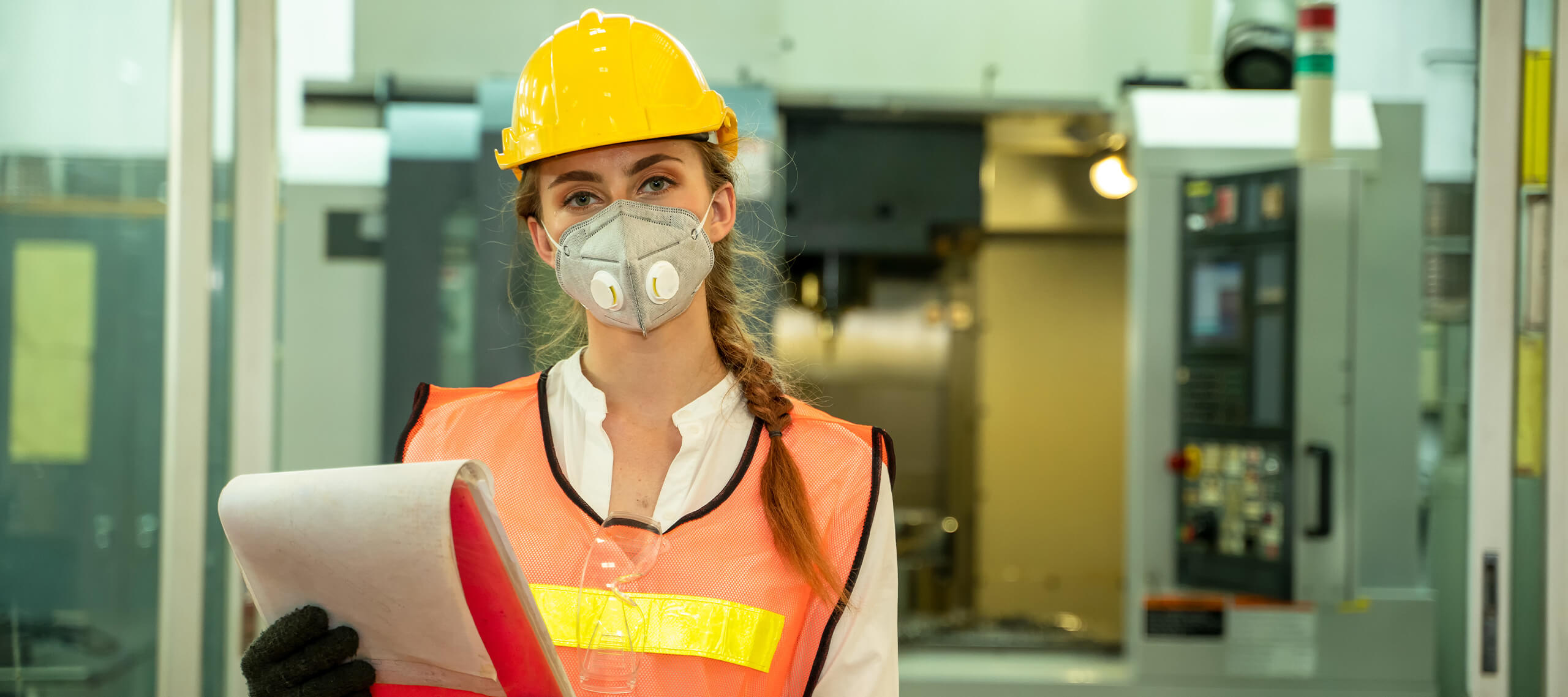
Protective Equipment: A Broad Category
Our response to the unprecedented shortage of face masks and shields in U.S. healthcare facilities was rapid. Global Thermoforming excels at providing quick production times, thanks to our range of capabilities. With turnaround times as short as 2-3 weeks for thin-gauge components, we were available to step up and provide needed equipment.
Getting these PPE components into the hands of healthcare workers is a priority. The airborne particles that are associated with sneezing, coughing, or in the intubation of patients put them at extreme risk. Our teams went to work to create effective protection. We created three mask prototypes – both single-use and reusable – that are brand new and completely innovative. These can be manufactured within the U.S. and will avoid the shipping delays that plague the delivery of imported products.
However, masks are just one part of the defense against the COVID-19 virus. Our locations also manufacture items such as plastic barriers for grocery stores, mobile sanitizing sinks, hospital tabletops, work surfaces, storage, and more. We’ve been able to modify our output to meet the needs of the medical industry and essential supply chains thanks to the innovative use of our CNC machines and thermoforming equipment, such as our Sencorp 2500 machine. When the high demand for critical parts and equipment was made public, we were in a position to help – quickly and skillfully.
Taking Care of Our Most Important Assets
The safety and health of our employees were on our minds long before the full COVID-19 pandemic occurred. As an essential business, we knew that we would not only continue to operate but that we could get even busier. There was no time to waste in setting up the new procedures to protect our staff at our manufacturing plants. Ensuring that our customers received the best products safely and our high-quality standards remained intact was and still remains a priority.
“We have taken on new clients to help with the medical needs of our company. Because of the outbreak, we are greatly reducing our contact with the outside world and other companies until COVID-19 is behind us.”
Adam Bergauer | Owner of Global Thermoforming
Global Thermoforming rapidly implemented several changes, all designed to address the issues of employee safety. All of our systems have been improved, from office procedures to the way we package items.
In our offices, we’ve offered the opportunity for 100% remote work for our staff. Washing hands once per hour is a requirement of all our employees while on the job during their required break. We have allowed some of our team to work shorter shifts, and they must stay home from work if feeling unwell. We expect our employees to observe the recommended social distancing protocols while on the job.
The working environment is also closely monitored. We regularly clean our machines using a DOD-approved sanitizer, and we’ve also made changes to ensure that each product leaves our factory is clean and sanitized. Each package is prepared by one person at the plant, who wears gloves and a mask while doing so.
We’re proud of our employees and are immensely appreciative that they’re part of the Global Thermoforming team.
“I’m very grateful to have a paycheck and be working at Global Thermoforming during this pandemic. We feel very safe at work, we are taken care of well. It's an honor to do our part in making new medical products that will hopefully help save people and stop the spread of the virus.”
Global Thermoforming Employee
As we move forward through this challenging time, our team is aware that we are part of the solution. With each employee that we keep safe, each procedure that we implement to keep our facilities and products clean and healthy, and each product that we produce to help combat the pandemic, we are both proud and thankful to continue providing quality thermoforming services.
At Global Thermoforming, we stay involved through the entire process, and our ability to produce large parts with thin walls in a variety of shapes has led to the use of thermoforming in many diverse industries we serve. Including Aerospace Components, Medical Components, Bath & Shower Furnishings, Pools & Spas, Recreational, Vehicle Components, Sidings & Windows, Consumer Products, Appliances and Housewares, Automotive Components, Marine Components, Lawn & Garden, Agricultural Components, HVAC Components, Disposable Packaging. Contact us to learn more about Global Thermoforming.
Have an upcoming project?
Whatever your manufacturing needs may be, Global Thermoforming can put our engineering, design, and manufacturing expertise to work for you.