How Much Does Thermoforming Cost?
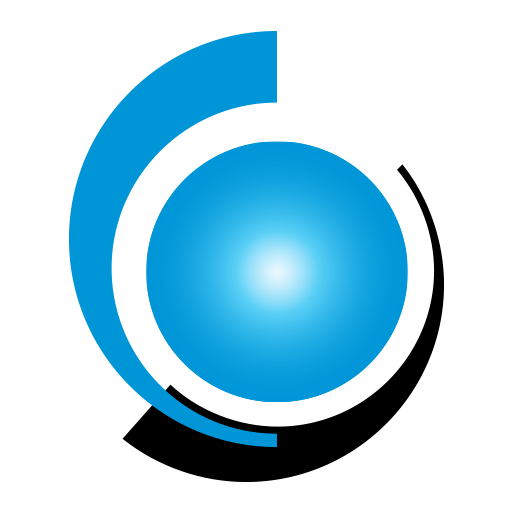
Thermoforming is an efficient, versatile, and fast way to manufacture products. At Global Thermoforming, we work with a vast range of industries – creating components for everything from aircraft interiors to food packaging. After more than 30 years of manufacturing experience, we know what questions we hear the most from new clients. Needless to say, one of them is: “How much does thermoforming cost?”
The cost of thermoforming is dependent on several factors. In producing a product, factors such as the initial design and prototyping, mold making, material selection, finishing, and labor are all unique to the project. To help explain how these work together in determining costs, let’s look at what goes into thermoforming.
Unlike injection molding, thermoformed plastics are created from a single sheet of flat plastic. It’s first heated, then vacuum is used to form the specific part or in some cases, we use air pressure to help assist the vacuum. Once cooled, it’s removed from the mold, trimmed, and finished. At this point, additional steps such as CNC routing, fastening, decorating, painting, printing, and labeling can take place.
Although the thickness and type of plastic can vary, the process of thermoforming is the same – whether making a cupcake tray or an automobile dash cover. Let’s discuss each element of the journey from the drawing board to the end of the production line – and see how costs are calculated.
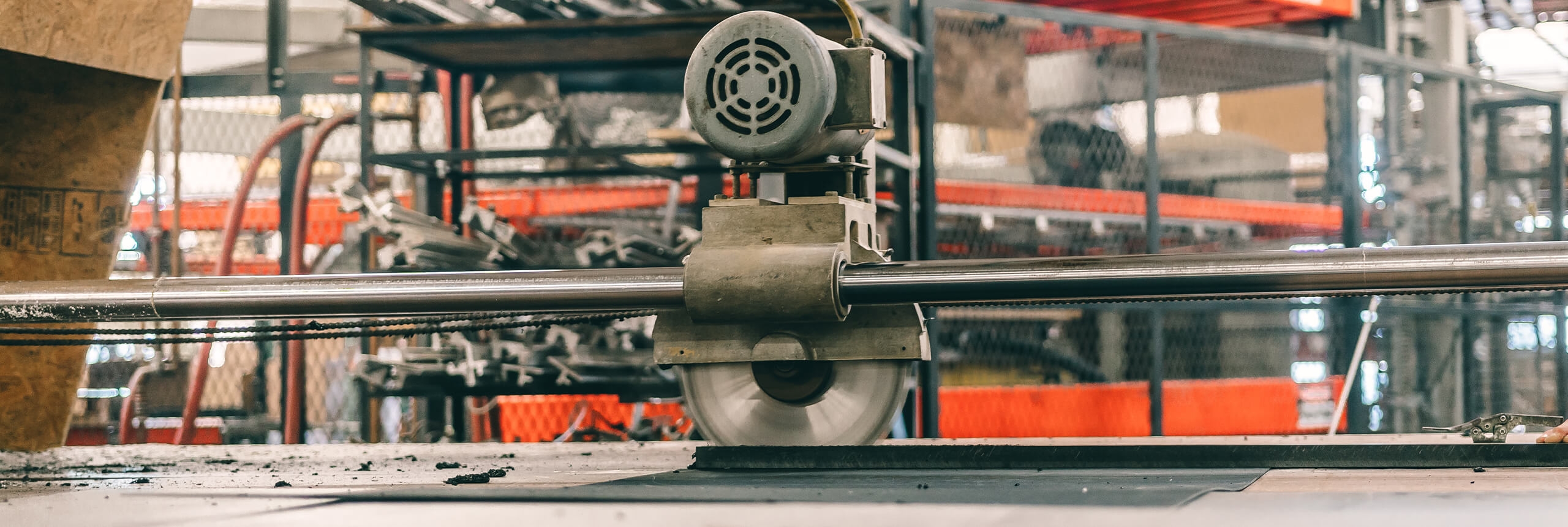
Design and Tooling
Our engineers start a project working with clients to design, or tool, the thermoforming mold for their part. Each mold is created from scratch to exact specifications, that are unique to the component. Pieces can be relatively simple or exceptionally complex, with dimensions that range from centimeters to beyond 11 feet.
With thermoformed plastics, the tooling process takes 1-6 weeks (depending on prototype/production tools), and the costs per mold can range between hundreds of dollars to thousands of dollars. We utilize several mold options to best suit your particular project – factors such as longevity, complexity, and the run size can all play a part in this choice.
Another cost factor related to design and tooling is part geometry. As thermoforming uses single sheets of plastic, it’s important to create the maximum number of parts from every piece. Although this doesn’t seem evident at the outset, good design helps pay for itself by minimizing trimming and waste.
Additionally, at our facility, we can adapt injection-molding designs into thermoforming. The thermoforming process can be 4-5x less expensive than the tooling charges associated with injection-molded products. It’s essential to consider these secondary benefits when considering costs.
In short, there’s value in what an experienced manufacturer can bring to a project in reduced prototype production times, maximized use of raw materials, and innovative design.
Materials
Whether utilizing thin-gauge plastics (under .06″ thick), or thick-gauge (up to 1″ thick), your materials costs are determined per sheet. We use a wide range of plastics, including those that are suitable for heavy-duty applications. Materials such as polycarbonate, ABS, HDPE, HMWPE, Kydex, and Royalite are used for producing components for aerospace, medical, shipping, and other industries.
If you’re curious about whether your project will require a thin or thick-gauge plastic, we introduce some of our materials here on our website. We’re also happy to talk to you about your particular needs, and what your part may require in terms of tolerance, impact strength, temperature resistance, and more.
With the wide range of plastics that are available to our customers, the price per sheet can range between pennies to thousands. The Global Thermoforming engineering team can be a vital part of the materials selection process, using more than 50 years of experience to help keep your costs down and our pricing competitive.
Secondary Operations
The costs of thermoforming may have additional operations or processes to consider. Once the thermoformed sheets have gone through the molding process, they can require trimming and further steps to be taken. Our manufacturing facilities can provide many secondary options in-house, helping you create highly customized parts and packaging.
Our CNC trimming and finishing capabilities are part of the quality-driven services we provide – but they’re not the end of the line.
Before they leave our factory floor, parts can be painted to create texture, improve electrical conductivity, match colors with adjacent components, and more. We also can apply labels, use screen, laser, and offset printing on surfaces to add information or decoration, and add fasteners with press and snap fittings, bonding, or ultrasonic welding. We also offer packing and shipping of products, providing a genuinely turn-key experience for our customers.
As you can see, thermoforming costs have many components and a lot of variables. Fortunately, we have the manufacturing experience and commitment to customer service to walk you through price quotes in a way you’ll understand. We’re here to exceed your expectations, and welcome your questions!
At Global Thermoforming, we stay involved through the entire process, and our ability to produce large parts with thin walls in a variety of shapes has led to the use of thermoforming in many diverse industries we serve. Including Aerospace Components, Medical Components, Bath & Shower Furnishings, Pools & Spas, Recreational, Vehicle Components, Sidings & Windows, Consumer Products, Appliances and Housewares, Automotive Components, Marine Components, Lawn & Garden, Agricultural Components, HVAC Components, Disposable Packaging. Contact us to learn more about Global Thermoforming.
Have an upcoming project?
Whatever your manufacturing needs may be, Global Thermoforming can put our engineering, design, and manufacturing expertise to work for you.