Which Plastic Materials Are Used In Thermoforming?
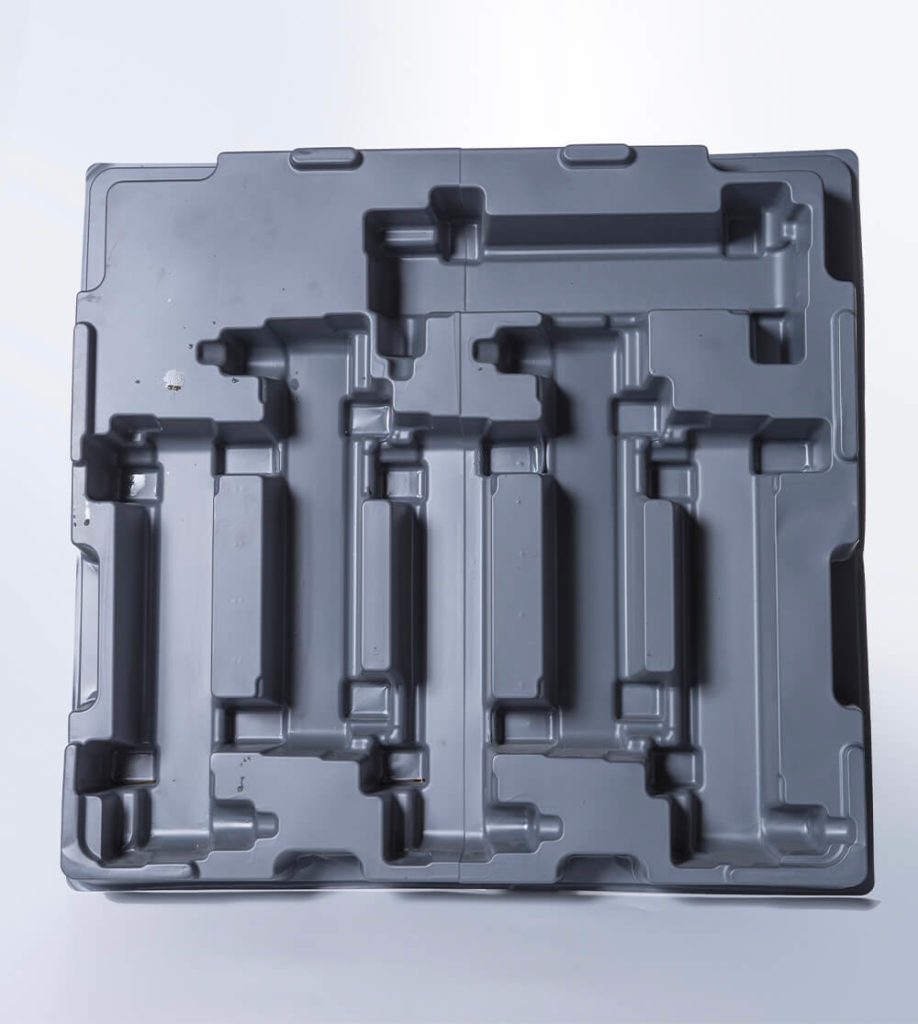
Although all the thermoformed plastics we use are high-quality, there’s an incredible range and diversity of types. Since we manufacture products with both thick and thin-gauge plastic, we work with many different types. This month, we’d like to explore the range of available materials and discuss what makes them suitable for different applications and industries. Here at Global Thermoforming, we have the hands-on experience and knowledge to help our clients produce the highest quality components.
Thermoforming plastic sheets can use many types of material – but there are some key characteristics to consider. Factors like transparency, hardness, rigidity or flexibility, and impact strength help manufacturers select the right thermoplastic for each part.
We work with both thick and thin gauge plastic sheets in our plastic manufacturing locations. Both are heated in an oven to a temperature that allows it to be expanded in or over a mold and then cooled to a completed shape. We know this simplified version as vacuum forming. However, the plastic materials used for a clamshell packaging piece will have completely different requirements than what we will specify for a plastic pallet!
Let’s take a look at some common plastic materials used in thermoforming and some basic characteristics of each. The “Thick + Thin” designation after each plastic’s name indicates its suitability for Thick or Thin Gauge uses.
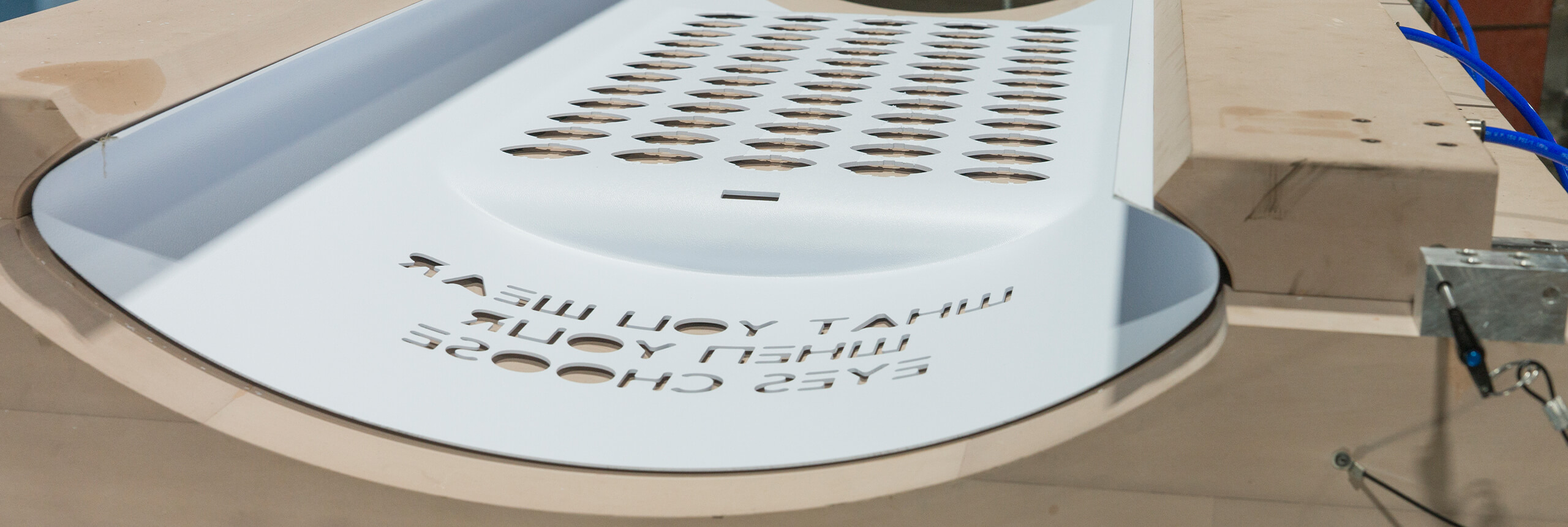
ABS (Acrylonitrile butadiene styrene)
ABS (Acrylonitrile butadiene styrene) (Thick + Thin) is a low cost and versatile plastic. It offers toughness without heaviness and is used in various consumer products, from toys to machine housings.
Acrylic
Acrylic or (polymethyl methacrylate) (PMMA) (Thick) is a material that many are familiar with – think of brand names such as Lucite, Perspex, and Plexiglas. The range of uses for this transparent plastic work for various industries that need transparency and strength. It is optically clear and resistant to weather and abrasion. With its similarity to glass, acrylic is used in everything from instrument panels and aircraft windows to safety shields, outdoor furniture, helmet visors, windshields, and retail displays. Acrylic can also be specified in colors, the amount of opacity, texture, and more. Lighter than glass and superior in impact resistance, the various grades of this material make it versatile and easy to machine, bond and fabricate.
HIPS (High Impact Polystyrene)
HIPS (High Impact Polystyrene) (Thick + Thin) is easy to thermoform, easy to mold and fabricate, and is available at a less expensive cost than some other options. Tough and printable, it’s popular for retail countertop displays, picture frames, food containers, and even shower walls. It can also be machined and assembled easily, using mechanical fasteners, adhesives, or solvents.
Kydex
Kydex (Thick + Thin) is a thermoplastic that can be customized for appearance while staying extremely tough – airplane interiors would be a great example of its use. At Global, we produce medical devices and other pieces that require special textures and customized colors. The versatility of Kydex creates aesthetically, pleasing and durable products.
Nylon
Although Nylon’s (Thick) associated with the fibers used in fabrics and other materials, it is also used for mechanical parts. In thicker gauges, this material is utilized in the automotive industry for machine screws, gears, and gaskets formerly made of metal. Nylon is also used in combination with other materials, such as carbon and glass fibers, to make heat-resistant automotive components. It’s also utilized for food packaging films that require an oxygen barrier.
PC (Polycarbonate)
PC (Polycarbonate) (Thick + Thin) plastics are known under several trademarked names such as Lexan and arcoPlus. This transparent material impacts resistance, optical clarity, and stiffness and is easy to fabricate and machine. As you might expect, it’s a versatile material that’s utilized in many industries. Electronic components, data storage devices, machine guards, signs, construction materials, automotive and aircraft parts, and much more are popular uses for Polycarbonate.
PE (Polyethylene)
PE (Polyethylene) (Thick + Thin) plastics are a group of materials that vary in density – allowing for a huge range of uses in thermoformed products. Moisture-resistant and non-reactive to many chemicals, you’ll see it in everything from clear plastic bags to medical and defense industry components. Durable polyethylene offers a high strength-to-density ratio, making it a popular choice across many industries. You may see products ranging from water storage and liquid containers, outdoor furniture, medical radiation shields and outdoor equipment enclosures made of HDPE (High-density Polyethylene) to ballistic armor, hydraulic seals and bearings, and marine infrastructure components that utilize HMWPE (High-Molecular Weight Polyethylene) thermoformed materials. Other varieties include lower density materials such as MDPE (Medium-density Polyethylene) and LDPE (Low-density Polyethylene).
PEI (Polyetherimide Ultem)
PEI (Polyetherimide Ultem) (Thick) is another thermoplastic that offers high heat resistance and strength. As you might expect, they are often used to manufacture components such as microwave parts and under-the-hood automotive items.
PETG (Polyethylene Terephthalate Glycol)
PETG (Polyethylene Terephthalate Glycol) (Thick + Thin) is a transparent plastic sheet forming material with a lower forming temperature. It’s easy to vacuum and pressure form and offers chemical resistance. However, it’s less UV-resistant than some other plastics. It’s useful for structural automotive parts, hand tools, and interior signage.
Polytetrafluoroethylene
Polytetrafluoroethylene (Teflon) is well-known for its hydrophobic (water-repellent) properties. While its presence in cookware is well-known, Teflon is also a key component of bearings and supports moving parts in machines, such as Belleville washers. The latter use is related to another of Teflon’s key qualities – it has an extremely low friction rating. High chemical resistance is another feature of this material, making it a popular choice for corrosive chemical containers.
PLA (Polyactide)
PLA, or polylactide, (Thin) is compostable and made from renewable resources, such as corn starch. This is a versatile “bioplastic” used for products like cutlery, food and beverage containers, and disposable pens.
PP (Polypropylene)
PP (Polypropylene) (Thick + Thin) is useful for many products and is a recyclable plastic (Number 5). It’s well known as the material for reusable food containers, including those suitable for dishwashers and microwaves, as well as a huge range of household and industry products. PP offers chemical resistance that makes it a popular choice for laboratory parts, acid tanks, piping systems, and more. It’s easy to customize and dye, lightweight, and unlikely to shatter. However, it’s not as UV-resistant as some other thermoplastics.
PVC (Polyvinyl chloride)
PVC (Polyvinyl chloride) (Thick + Thin) is a familiar name to many. Its high impact strength is ideal for piping systems and tanks. It offers high chemical and stain resistance, natural flame retardant qualities, and is easy to fabricate. Products made from PVC include packing and shipping trays, clamshells, housing materials, telecommunication items such as wires and cables, and even cabinets and working surfaces. The thin and thick gauges of PVC offer maximum versatility for a range of industries.
Royalite
Royalite (Thick + Thin) thermoplastic is used for many medical, aerospace, automotive, and electronics applications where impact strength and heat resistance are paramount. You’ll see Royalite used in components such as equipment housing, cleanroom wall coverings, aircraft interiors, and automotive casings. It offers a tremendous range of colors and can also be painted. With both high formability and finishing possibilities, Royalite is available in a diverse portfolio of materials.
TPO (Thermoplastic Olefin)
TPO (Thermoplastic Olefin) (Thick) is known for its high impact strength at even cold temperatures and other features such as chemical resistance, stability, and stiffness. For parts exposed to extreme weather conditions and outdoor usage, TPO is ideal. You’ll see it used for automotive applications such as car bumpers and other components, where the available high gloss finish adds to its appeal. The toughness of TPO also makes it popular for chemical shield and gear covers, where it withstands harsh conditions easily.
The range of different plastic materials available for your next thermoforming project is broad, but we’re happy to help you find the right one here at Global Thermoforming. We’re more than just experts at thermoforming plastic – our team has the experience to specify and source the best materials for your project’s components! Discover the potential for your project by contacting us today!
Have an upcoming project?
Whatever your manufacturing needs may be, Global Thermoforming can put our engineering, design, and manufacturing expertise to work for you.