Plastic Thermoforming: Expectations vs. Reality
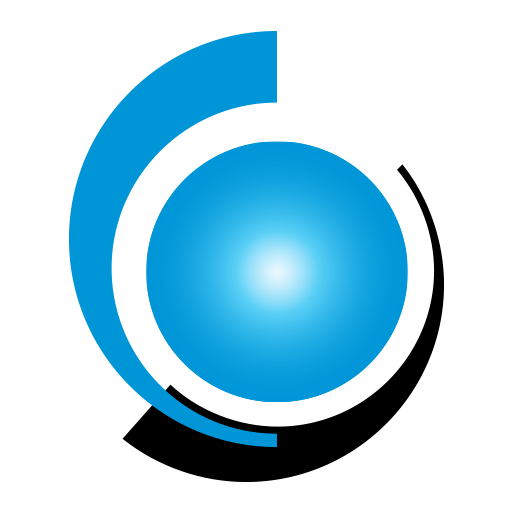
Plastic thermoforming is a well-established process for creating a wide range of consumer products. As the demand for plastic increases, so does the need for more efficient ways to produce plastic parts. In particular, as demanding injection molding requirements have been increasing due to the increasing use of recycled plastics and other environmental pressures, thermoforming has been seen as a potential way to increase production efficiency.
There is a lot of hype around plastic thermoforming, with many people expecting it to be the silver bullet for increasing production efficiency. However, as with any new technology, there are often unrealistic expectations about what it can do. In this article, we will take a closer look at the reality of plastic thermoforming and explore the benefits and limitations of this process.
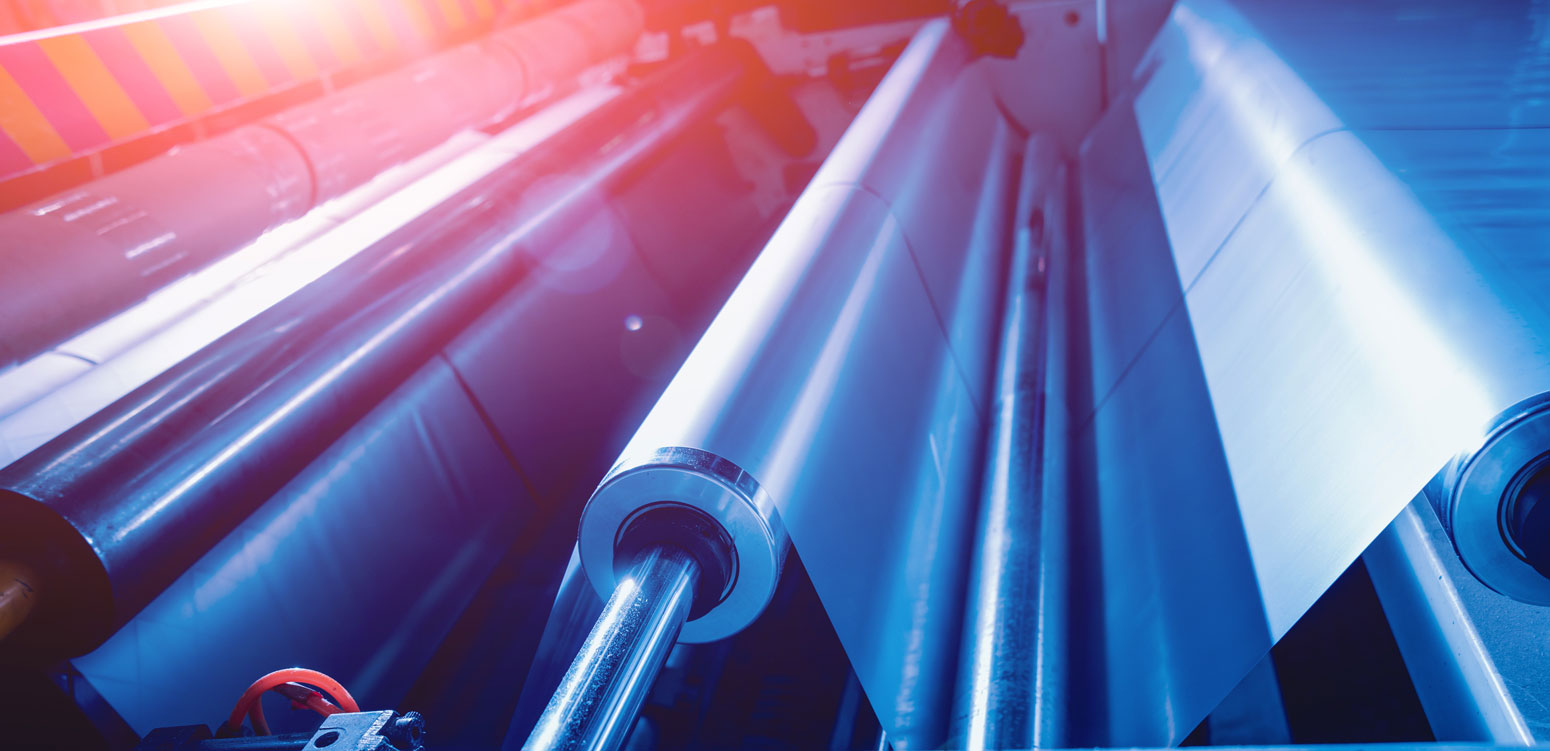
What is Plastic Thermoforming?
Thermoforming is a process that uses heat to shape plastic into a variety of products. First, the plastic is heated until it becomes soft, and then it is formed into the desired shape. This process is commonly used to create packaging materials, consumer products, and more.
Plastic thermoforming is different from injection molding in that it does not require expensive tooling to produce the desired shapes. Instead, the heating rod of the forming press serves as a form for each part being made. The ability to use existing equipment without creating or purchasing expensive new tooling is one of the main advantages of plastic thermoforming
How Does Plastic Thermoforming Work?
Understanding how plastic thermoforming works is helpful first to understand injection molding basics. Injection molding is when molten plastic is injected into a mold cavity. The mold cavity is then cooled, and the plastic solidifies into the desired shape.
In contrast, the plastic is heated until it becomes soft in plastic thermoforming. It is then placed on a forming rod, which serves as the mold cavity. The hot plastic conforms to the shape of the forming rod, and then it is quickly cooled. This cooling process causes the plastic part to hold its new shape.
This process can be done with either flat stock or pre-preg, depending on the desired thickness of the part. Once formed, the shaped plastic sheet is trimmed and transferred to a stacker for further processing or packaging.
Benefits of Plastic Thermoforming
The main benefits of plastic thermoforming include the following:
Lower tooling costs: Injection molding requires expensive manufacturing tools. Plastic thermoforming does not rely on a mold but rather a heating element already used for other purposes. This means that it can utilize existing equipment without purchasing new machinery.
Greater design freedom: Thermoforming does not require expensive tooling to produce plastic parts. Instead, existing equipment is used to form the desired shapes. This means that industrial designers have greater flexibility in creating products with the materials they want since there are no restrictions on whether or not they can be manufactured through injection molding.
Faster cycle times: When a part is injection molded, the mold must be cooled between each part. This process can take up to an hour, significantly slowing production down. In contrast, plastic thermoforming does not require a tool change, so it has faster cycle times and is more efficient overall.
No core pulls: Injection molded parts often have to be cooled in the mold for some time until they are strong enough to be removed. After that, they must then undergo secondary processing to remove the part from the expensive injection molding tool. Since thermoformed parts do not require these steps, there is much less waste and downtime in production.
High-quality surface finish: One of the main disadvantages of injection molding is that it can often leave a textured surface on the finished parts. This is due to the cooling process, and the molten plastic flows into the mold cavity. In contrast, thermoforming results in a smooth surface finish on parts, advantageous for specific applications.
Disadvantages of Plastic Thermoforming
Plastic Thermoforming Cost Analysis
The different costs involved must be analyzed to determine whether it is economical to utilize plastic thermoforming for a specific application. A typical cost for thermoforming includes material and labor. In addition, tooling may need to be purchased or manufactured to form the desired shapes, and there are also heating and cooling costs associated with the process.
The costs of injection molding must also be considered. Injection molding is often more expensive initially, but the tooling can produce many parts. However, it is essential to note that injection molding can also be cheaper for high-volume manufacturing.
When comparing the total costs of forming to injection molding, there are certain cases where thermoforming is more economical. For example, if plastics thermoforming manufacturers have existing equipment that can use heating elements to form parts, it might be less expensive than purchasing dedicated tooling. In other cases, where the number of parts to be produced is low or the complexity of the part is high, injection molding may be more advantageous.
Thermoforming: Expectations vs. Reality
Plastic thermoforming has become an increasingly popular alternative to injection molding in recent years. This process does not require the use of a mold but rather a heating element that is already used for other purposes. This means that it can utilize existing equipment without purchasing new machinery.
However, many misconceptions about plastic thermoforming can make it difficult to determine whether this process is suitable for a specific application. In addition, the advantages and limitations of plastic thermoforming do not always live up to expectations. This article aims to clarify some of these misconceptions and provide greater clarity on how this process compares with injection molding.
No matter what type of plastic part is being manufactured, it must be appropriately designed to function the way it was intended. If you need assistance with your design for manufacturing or looking to reduce your overall costs, contact our experts today! We’ve helped many clients achieve their goals through injection molding and plastic thermoforming.
Some unrealistic expectations about plastic thermoforming are that it can always reduce cycle times, improve quality, and even eliminate the need to make prototypes. While these benefits may be realized under certain circumstances, many limitations should be considered before transitioning from injection molding. There are solutions to help with these problems, including using plastic injection molding for small production runs.
Factors limiting the success of plastic thermoforming include surface finish, part weight, dimensional tolerances, and gate location. The thickness of each part may also change during the process due to cooling effects.
The Top 7 Myths Explained
The Top 7 myths about plastic thermoforming are as follows:
1. Thermoformed parts are always less expensive than injection molded parts.
2. Parts can be quickly and easily produced with no tooling expense.
3. The quality of thermoformed parts is always better than injection molded parts.
4. The surface finish of thermoformed parts is always superior to injection molded parts.
5. Thermoforming is a quick and easy process that does not require any specialized knowledge or equipment.
6. All parts can be successfully thermoformed.
7. Thermoforming can eliminate the need for prototypes.
While it is true that thermoforming can often be less expensive than injection molding, it should be noted that this is only true for one-time production runs of less than 5,000 parts. If the number of components to be manufactured increases past this threshold, several factors make plastic thermoforming more expensive.
Surface finish is often superior to injection-molded parts because these parts are typically made from a single piece of plastic. On the other hand, Thermoformed parts are cut from a plastic sheet and then assembled. This can lead to inconsistencies in the surface finish and an overall lower quality product.
Dimensional tolerances are also better with injection molded parts because they are formed in a mold. This means that the part begins as a solid plastic block and then is forced into perfect shape by the mold. The material must first be heated to a very malleable state with thermoforming before forming around a heating element.
In addition to the drawbacks discussed above, a few misconceptions about plastic thermoforming should be clarified. Some of these myths include the following:
1. All parts can be successfully thermoformed- While this is true for many applications, certain products require a more sophisticated manufacturing process better suited for injection molding.
2. Thermoforming can eliminate the need for prototypes- This may be true in some cases. Still, a prototype is often necessary to verify the feasibility of the design and test the functionality of the part.
3. Parts can be quickly and easily produced with no tooling expense- Thermoforming is typically more expensive than injection molding because it requires specialized equipment, but this does not mean that the process cannot be cost-efficient.
4. The process is quick and easy- While thermoforming can often reduce cycle times due to less complex tooling, the overall process still requires a significant amount of preparation and setup.
Have an upcoming project?
Whatever your manufacturing needs may be, Global Thermoforming can put our engineering, design, and manufacturing expertise to work for you.