Thermoforming vs Fiberglass
We have gotten the question, "thermoforming vs fiberglass, which one is better?" Thermoforming and fiberglass are similar processes. Both have low startup costs compared to other methods, allowing cost-effective creation of lower quantities of parts. However, they also have some definite advantages and disadvantages. The charts below will help you understand the differences.
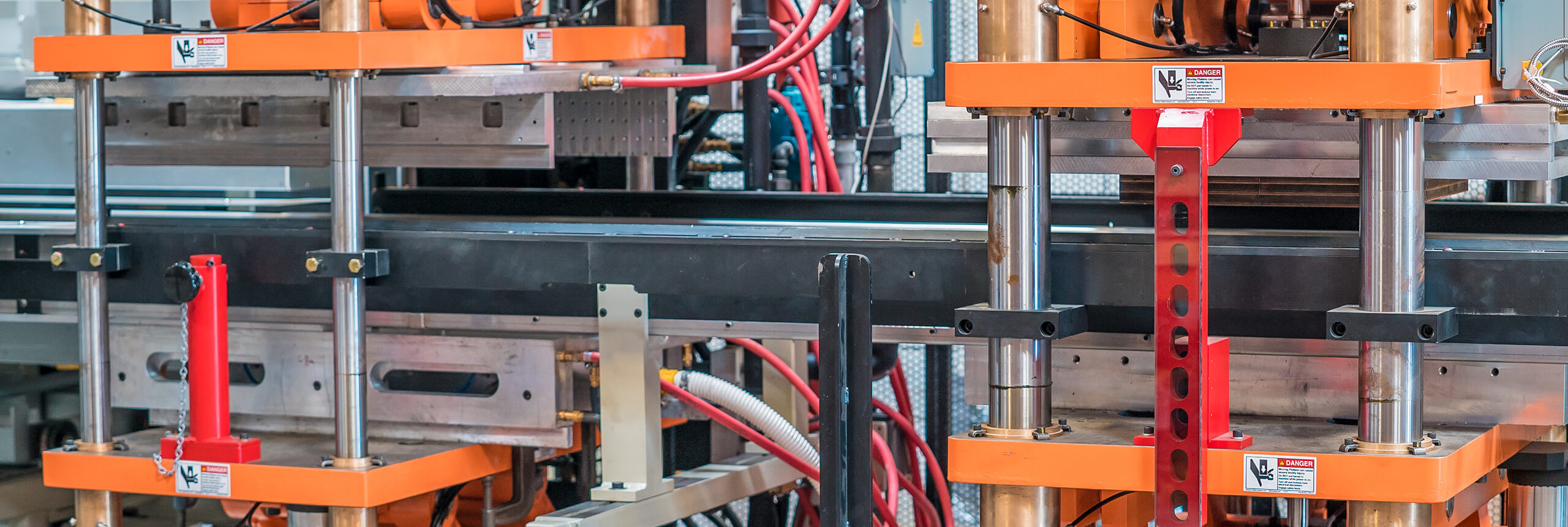
Thermoforming | Fiberglass | |
Fiberglass | A plastic production process that heats a rigid 2D sheet and uses a vacuum and pressure to form the plastic sheet (various materials) against a mold into a 3D shape. | Process in which fiberglass reinforced resin plastics are formed into 3D shapes. The process usually involves making a mold and then using the mold to make the fiberglass component. |
Volume | Production volumes from hundreds to mid thousands. Thermoforming is the most cost-effective method out there. | Fiberglass is typically used for smaller runs and prototyping. |
Material | HDPE or HMWPE (Polyethylene) is a popular material choice for replacing fiberglass. HDPE or HMWPE (Polyethylene) is more durable, crack and UV resistant and significantly lighter when compared to its fiberglass counterpart. | There are limited choices when it comes to Fiberglass material. The options are typically limited to fiber materials, fiber weave and either polyester or epoxy composite materials. |
Finished Part Weight (See Specific Gravity Graph) | 35% Lighter than Fiberglass | 35% Heavier than Thermoformed parts |
Finishing Options | Molded with color and texture options. | The finished part needs to be painted. |
Recyclability | Final thermoformed parts and the excess material produced after CNC Trimming are fully recyclable. | Final parts are non-recyclable, and the Fiberglass production process uses a large amount of hazardous materials. |
Labor Costs and Lead Times | Thermoforming is an automated process. Most parts are formed from an aluminum tool, helping to decrease lead times and keep labor costs low. Thermoforming is faster and less expensive in high volumes compared to fiberglass processes. | Fiberglass molding is a labor-intensive process and more often than not requires multiple tools for the production of a single part. The result is slower production output, higher costs and longer lead times compared to thermoforming operations. |
Tolerances & Complex Geometry | Thermoforming can support the tight tolerances and complex geometries needed when creating mating parts. | Fiberglass processes are not as flexible when it comes to supporting complex geometries and tight tolerances needed to create mating parts. |
Part-to-part Repeatability | ||
Impact Resistance | ||
UV Resistance | ||
Molded-in Features | ||
Durability |
Specific Gravity of Thermoforming vs Fiberglass Materials
We use the specific gravity of a material to compare the weight of different materials. The lower the specific gravity of material the lower weight for an equal amount of material.
Comparing the specific gravity of conventional thermoplastics used in the thermoforming process against the specific gravities of routine fiberglass materials used in the fiberglass processes we can see that when wondering thermoforming vs fiberglass, thermoforming materials hold a distinct advantage.
Have an upcoming project?
Whatever your manufacturing needs may be, Global Thermoforming can put our engineering, design, and manufacturing expertise to work for you.