Thermoforming vs. Injection Molding
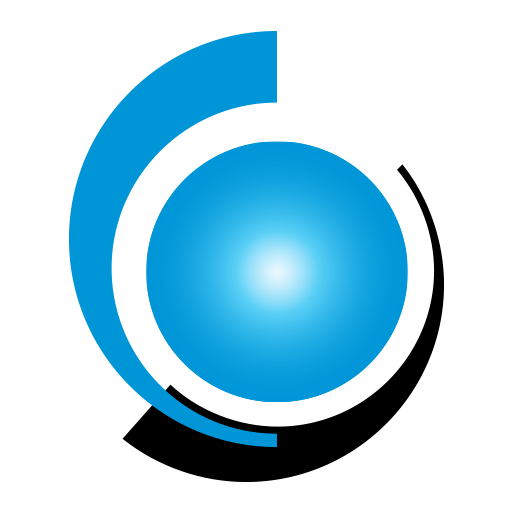
When our clients develop project ideas, they may have many questions about the differences between thermoforming vs. injection molding. It’s understandable – both of these processes have specific applications in manufacturing plastic components. In this article, we will provide an overview of how they compare with each other and take a closer look at key differences in particular areas, such as production times and costs.
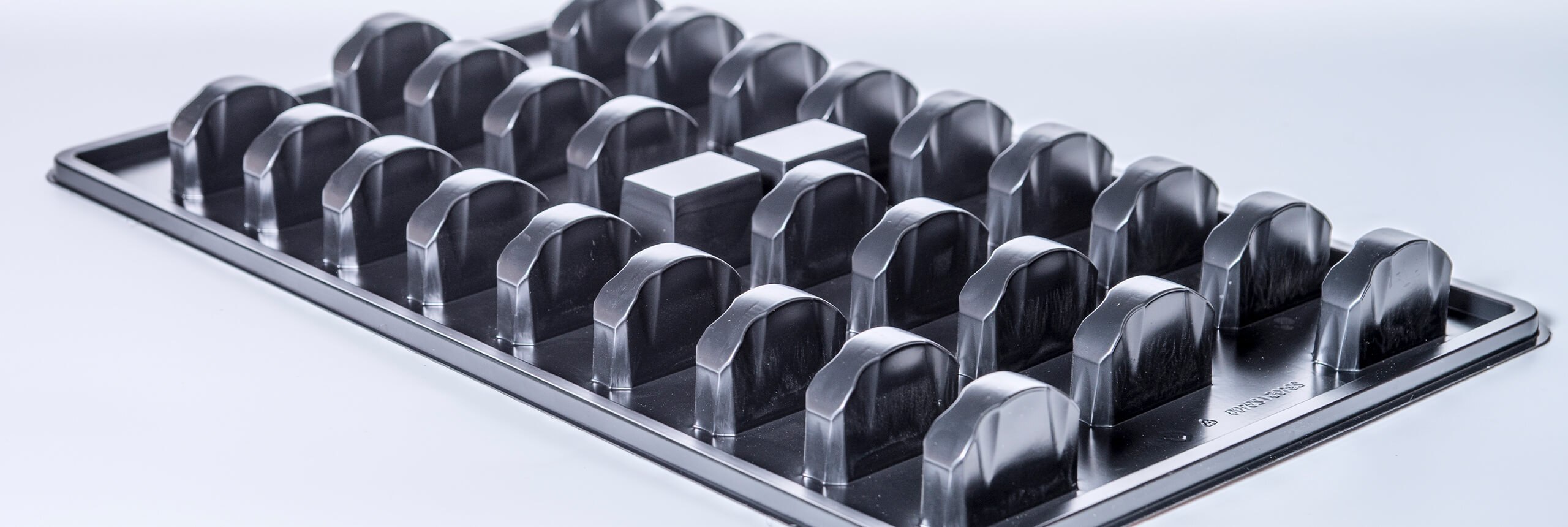
Basic Manufacturing Principles
Let’s start with the fundamental processes. Although both manufacturing methods work with heated plastic and molds, they use very different approaches to produce the final product.
Thermoforming works with flat plastic sheets and rolls that are softened using a heating process. Once pliable, they are molded into a male or female form using vacuum or a combination of pressure and vacuum forming.
The resulting three-dimensional piece is then trimmed and finished. At Global Thermoforming, we utilize our lineup of 3-axis, 4-axis, and 5-axis trimmers to remove excess plastic and create any holes, cutouts, or other design features for our clients.
Post-production, the individual pieces can be used as they are, or the pieces can have silk screening, paint, or specialty coatings applied. We work with both thin and thick-gauge thermoforming. Global Thermoforming produces everything from clamshell packaging and food trays to retail packaging and material handling pieces with thin-gauge thermoforming. Our thick-gauge products include items such as automotive interiors/exteriors, aerospace interior components, shipping pallets, and medical devices.
Injection molding uses a different approach to forming heated plastic. Instead of plastic sheets, plastic pellets are used for the raw material. They’re fed into a hopper and heated within the machine to a liquid state. Then, using extreme pressure, they’re injected via a nozzle into a double-sided metal mold. The machines used for this process are called presses. After cooling, the finished piece is ejected from the mold.
At this point, many injection molded parts are painted, or have additional finishes applied. Silkscreening, sandblasting, and polishing are all commonly used. Injection molding also creates finely detailed components and pieces with multiple wall thicknesses right out of the mold.
What does this all mean to your project? In manufacturing, thermoforming and injection molding have their benefits. Breaking down the differences between production costs, lead times, and other considerations are critical for the best outcome. Let’s look at the key comparisons.
Production Costs vs. Tooling Costs
The type of molds used in injection molding requires a much more extensive and expensive tooling process. As they typically are made of stainless steel, aluminum, or an alloy metal, and are double-sided, these molds are more costly and take longer to produce. Thermoforming molds can be made of other softer materials, are created faster, and have a much lower initial cost than injection molds.
On the production side, injection molding can have lower per-piece costs than thermoforming, pending on the part size. Injection molding is often used for high volume production runs where the small difference in the unit costs can be multiplied by thousands of units.
Summary: Injection molding can produce very high-quality parts and can have lower part prices but more expensive tooling costs. Thermoforming has a significantly less tooling expense and but can have a slightly more expensive unit cost. Based on our experience, in the thick gauge area (0.080” – 0.500” thickness), thermoforming usually makes sense when the EAU is between 2,000 and 5,000. Thin gauge thermoforming (0.008” – 0.030” thickness), such as clamshell and retail packaging where quantities can reach the millions of units, cannot be repeated by the injection molded process.
Timeline Factors
The time needed for both tooling and production is quite different between thermoforming and injection molding. With faster turnaround on producing both prototype samples and molds, thermoforming moves projects into production faster.
At Global Thermoforming, we can expect lead times of approximately 8-14 weeks from project start to completion: 3-8 weeks for tooling (pending on prototype/production tools), and 2-6 weeks of production (pending on the quantity). We can also produce prototypes in as little as two days. In comparison, a similar schedule for an injection molding project would run 24 weeks: 16 weeks for tooling the mold, and 8 weeks for the production run.
Summary: Thermoforming offers a substantially shorter window from concept to completion.
Other Considerations
A few more details can help you decide between injection molding vs. thermoforming for your project. The part size, variations in thickness, run size, and aesthetics of a product can also dictate which process is best for your company.
The fact that thermoforming works with large sheets of plastic make it suitable for a wide range of part sizes. At Global Thermoforming, we can produce parts in dimensions up to 11′ x 7′ with close tolerance forming. Using plastic sheets also allows us to consolidate several smaller components into a single large one. In comparison, injection molding can work with individual parts of up to 4′ x 4′, with no consolidation.
Variations in thickness are best handled with injection molding, due to how the plastic is forced into its mold. Thermoforming offers more limited options here.
Lastly, the aesthetics of a part can be critical. The types of plastics that we use in our manufacturing offer a much wider variety of colors, and the thermoforming process can create a broader range of textures.
Summary: You’ll need to consider the size, thickness, run size, and desired aesthetics of your product, with thermoforming allowing for larger pieces and injection molding, providing more flexibility with variances in wall thicknesses. In addition, each thermoforming company can have different capabilities.
When you line them up, both thermoforming and injection molding can produce the results you’re looking for. However, thermoforming offers clear advantages in lead time and tooling costs. To help compare other factors regarding thermoforming vs. injection molding, please contact us. We’ll be happy to discuss which is the best manufacturing process for your product and help you make an informed decision when choosing a thermoforming company to work with.
At Global Thermoforming, we stay involved through the entire process, and our ability to produce large parts with thin walls in a variety of shapes has led to the use of thermoforming in many diverse industries we serve. Including Aerospace Components, Medical Components, Bath & Shower Furnishings, Pools & Spas, Recreational, Vehicle Components, Sidings & Windows, Consumer Products, Appliances and Housewares, Automotive Components, Marine Components, Lawn & Garden, Agricultural Components, HVAC Components, Disposable Packaging. Contact us to learn more about Global Thermoforming.
Have an upcoming project?
Whatever your manufacturing needs may be, Global Thermoforming can put our engineering, design, and manufacturing expertise to work for you.