Thermoforming: What is the difference between Vacuum Forming and Pressure Forming?
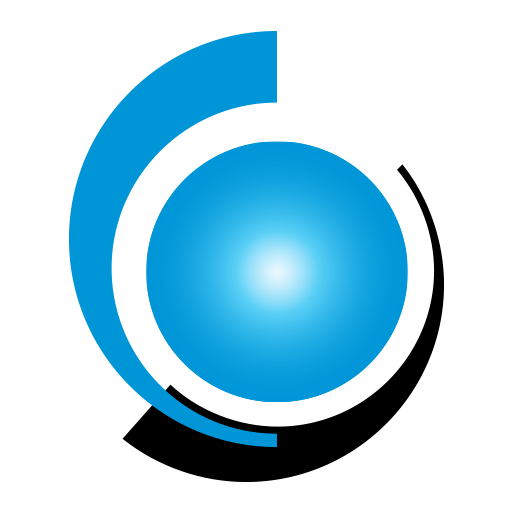
As a thermoforming company with over 30 years of experience, we know a lot about the subject! Previously, we’ve talked about some of the things to look for when you’re looking for a vacuum thermoformed plastic manufacturing partner. In this blog, we’ll take a closer look at the differences between thermoforming, vacuum forming, and pressure forming.
Thermoforming is a blanket term that covers more than one process. Using thick or thin-gauge plastic sheets, our factory heats them until they become pliable. The warm sheet is then molded to a form. On the most basic level, any type of thermoforming follows the same initial steps. The differences lie in how the molding is completed. As you might guess, both vacuum and pressure forming each have advantages for specific applications. Let’s explore these a bit more.
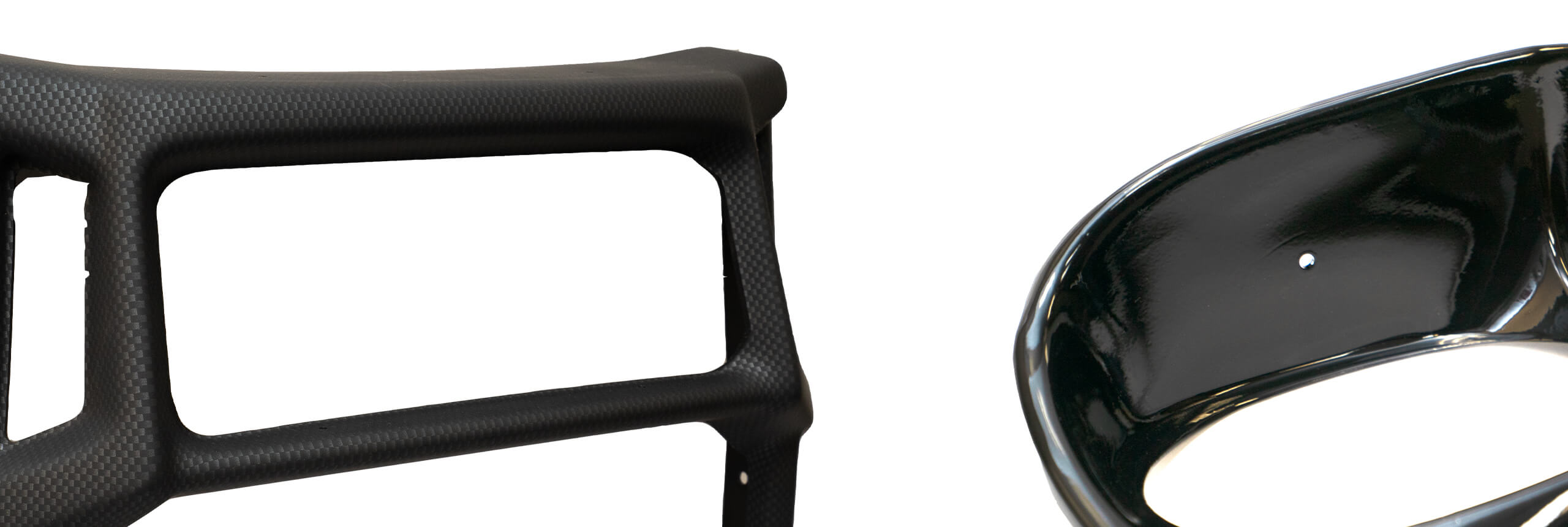
Vacuum Forming
To utilize the vacuum forming process, a sheet of thermoplastic material, such as PVC, ABS, HDPE, or PC, is first heated to a precise temperature, so it becomes pliable. Once the sheet is ready, vacuum pressure draws the hot plastic into or over the mold. The same vacuum pressure also removes all the extra air, pulling the material tightly onto the mold’s surface. This step creates a precise shape on one side.
The molds we use can be “female” – where the plastic is drawn into the mold – or “male” – where the plastic is formed over the mold. The choice of mold is dependent upon where the detailed elements are required. For example, an outward-facing panel requires additional details and textures. Here, a female mold design is best. Skilled designers, like our in-house team, are essential parts of the process, as they create the molds and ensure that there is close tolerance forming.
Overall, the sizes of the produced components can be small or large- the items can be as large as materials pallets or as small as instrument housing. Vacuum forming is fantastic for creating lighter, durable parts. These can often substitute for pieces made from heavier fiberglass or sheet metal. You can see examples of vacuum-formed components on fitness equipment, after-market car interior pieces, and pool and spa sections.
Pressure Forming
The differences between pressure forming and vacuum forming rely primarily on – you guessed it – air pressure, and the same step of heating a sheet of plastic kicks off the process. Working with materials like TPO, HIPS, or ABS, pressure forming uses compressed air to force the warm sheets of plastic into the waiting mold.
This higher pressure used creates components with greater surface detail and texture. If, for example, a piece needs lettering or an extra smooth finish, pressure forming is the ideal choice. Like vacuum molding, the details are kept to just one side of each piece. Mold designs can incorporate three-dimensional features and complex shapes. These configurations are ideal for applications such as multi-part assemblies, medical equipment, and control panels.
Pressure forming can compete with more expensive injection molding in many ways. It produces finely detailed pieces that can be moved onto the market much more quickly. Mold design time, less time spent tooling, and the ability to easily and quickly produce prototypes and smaller product runs are all benefits of the pressure forming process.
Final Touches
Both of these thermoforming processes still require finishing details, such as trimming. It’s best to trim the plastic components while they are still warm. For high-production items, this step is often completed while the plastics are still in the mold. Otherwise, the freshly-molded pieces are moved on to receive finishing touches, such as routing. Often, pieces are fastened with processes that incorporate mechanical fasteners, bonding with solvents or adhesives, or ultrasonic welding.
Items might also have printing or paint applied, or labels added. A real advantage of working with a thermoforming company is that the entire range of a component’s production can be kept under one roof. Both vacuum forming and pressure forming are highly efficient ways to get items into production and out in the market. Once the original molds are designed, and the type of plastic is selected, a company such as Global Thermoforming can keep everything moving in-house – from the production line to the finishing of each piece and even shipping. We love a challenge at our plants, such as our recent project creating Personal Protective Equipment for healthcare facilities.
If you have questions about which type of thermoforming is right for your project needs, our team is ready to help. With experience as the manufacturing partners for a long list of industries, we’ll be happy to assist you!
At Global Thermoforming, we stay involved through the entire process, and our ability to produce large parts with thin walls in a variety of shapes has led to the use of thermoforming in many diverse industries we serve. Including Aerospace Components, Medical Components, Bath & Shower Furnishings, Pools & Spas, Recreational, Vehicle Components, Sidings & Windows, Consumer Products, Appliances and Housewares, Automotive Components, Marine Components, Lawn & Garden, Agricultural Components, HVAC Components, Disposable Packaging. Contact us to learn more about Global Thermoforming.
Have an upcoming project?
Whatever your manufacturing needs may be, Global Thermoforming can put our engineering, design, and manufacturing expertise to work for you.