Top 10 Benefits of using Thermoforming
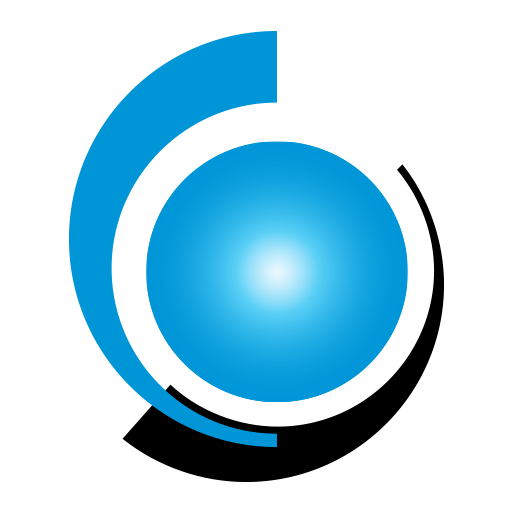
Thermoforming is a flexible, cost-effective, and fast process that is the cornerstone of materials manufacturing in packaging, transportation, technology, and more. As a quick review, this process takes a plastic sheet that is heated and then shaped using a mold to produce durable, high-quality products during production. With all the benefits this process offers, it’s no surprise that the range of products and applications adopting it continues to grow.
Check out the list below to learn about some of the top 10 benefits of thermoforming and how it could improve the manufacturing process for a variety of clients and industries.
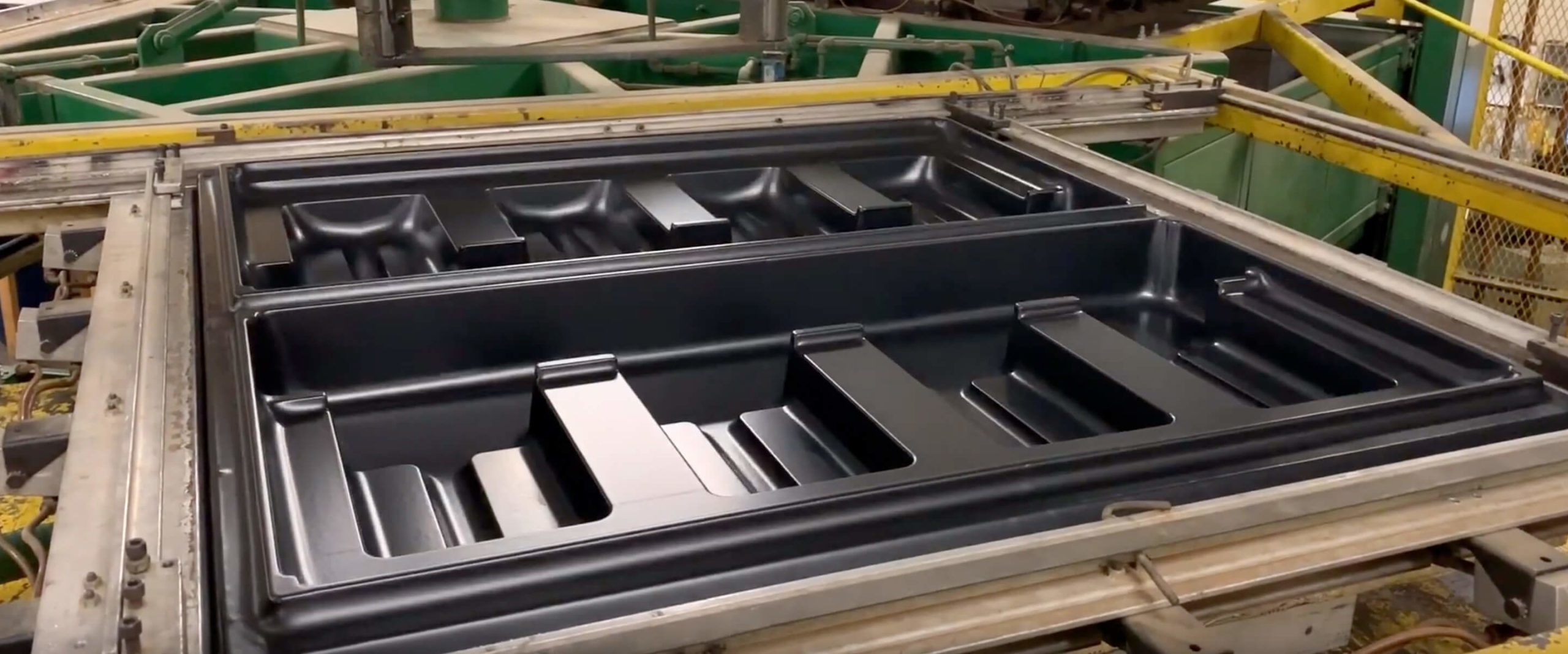
1 Various methods of thermoforming can fit any client’s specific needs
There is so much variation in shape, size, and complexity of plastic parts that it’s not a surprise that no single style of manufacturing will fit all of them well. However, the various thermoforming methods ensure that nearly any application has an ideal fit.
Vacuum Forming
During vacuum-forming, the heated plastic is stretched over a mold, and a vacuum removes the air forcing the plastic into the mold. This process is a fast and cost-effective approach to thermoforming and is often used when cost consciousness is high.
Pressure Forming
With this method, the heated sheets of plastic are pressed into shape around the mold. Because there is more direct pressure, the radii of the corners can be smaller, creating a sharper look for the edges of products, and is ideal for products with tight tolerances.
Twin Sheet Forming
This thermoforming method uses two sheets of plastics that are pressure-welded together to create the desired shape. Twin sheet forming is used in products that are hollow or double-walled.
Matched Mold Forming
Matched mold forming uses a male and female fold that come together to create a specific shape out of the plastic. Because two molds are used, the cost is higher than other options on this list, but the detail and specificity increase.
2 Thermoforming is used in nearly every industry
With the range of materials and processes available, thermoforming is flexible and can be used in nearly any industry imaginable. Some industries that currently use thermoforming in manufacturing and production are:
- Aerospace: Overhead storage bins, cup holders, armrests, machined accessories and components, lighting fixtures
- Agricultural: Hydroponic trays, plant pots, tractor panels, feed bunks and troughs, yard equipment
- Automotive: Door panels, exterior door panels, instrument panels, glove boxes, center consoles
- Medical: Face masks, mobile sanitizing sinks, hospital table tops, hospital drawers and cabinets, mobile X-ray equipment
- Packaging: Custom packaging, food packaging, cosmetics packaging, display packaging
- Technology: Autonomous vehicle panels, military drone aircraft, 5G cell phone tower covers, key cutting machines, consumer electronics packaging
- Windows and Siding: Window sills, skylights, home siding panels
This is only a partial list of potential applications, with the list of industries that participate in thermoforming far exceeding those presented here. One of the top 10 benefits thermoforming can apply to nearly any industry is that the thickness of the plastic is adjustable to fit the application requirements. For example, Thin Gauge Thermoforming generates plastic products less than .06 inches thick, and Thick Gauge Thermoforming uses thermoplastics for products between .06 and 1.0 inches.
3 Thermoforming can be faster than Injection Molding
In injection molding, liquid plastic polymers are “injected” into a mold using high temperature and pressure. Once the polymers have thoroughly cooled, they are removed from the molds. With the time it takes to fill the molds and the plastic polymers to cool from a liquid state to a stable solid, the process is slower than thermoforming and is less efficient.
Because of the speed of thermoforming, lead times and prototyping are significantly faster. The tooling process for thermoforming only takes about 3-8 weeks, with production completed between 2-6 weeks. As a result, the total lead time takes about 8-14 weeks from start to finish. However, the average injection molding lead time is around 24 weeks to complete production.
4 Thermoforming can use many materials, including sustainable alternatives
There are countless forms of plastic available for thermoforming, each with advantages ranging from natural flame resistance to high durability or chemical resistance. Each application can choose from a wide variety of materials to achieve the desired attributes. These materials include Acrylonitrile Butadiene Styrene (ABS), High-Density Polyethylene (HDPE), Polyethylene Terephthalate (PET), Acrylic, and Polyvinyl Chloride (PVC), to name a few. Here is a list of some of the common materials used by Global Thermoforming Inc. and their respective properties:
- Polyethylene – Thick/Thin: Excellent for products that need impact and chemical resistance and is well-suited for cold applications.
- Acrylonitrile Butadiene (ABS) – Thick/Thin: A very common thermoforming material with good stiffness and impact strength. Available in a wide variety of colors and textures.
- Polycarbonate (PC) – Thick/Thin: Very high impact strength and temperature resistance. Naturally clear.
- Polypropylene (PP) – Thick/Thin: Excellent chemical resistance, with high rigidity and impact strength. Dimensionally not as stable as other materials.
- Acrylic – Thick Only: An abrasion-resistant material that is easy to fabricate. Many colors are available and can be found in impact-modified grades.
As the world grows more conscious of environmental impact, more clients are looking for a sustainable option to meet their manufacturing needs. One sustainable option is to employ the use of bioplastics in thermoforming. Bioplastics are natural polymers derived from organic materials like sugarcane or corn, which are often biodegradable.
5 Thermoformed plastics can be recycled or reused
While not all plastics are biodegradable like the bioplastics mentioned above, many materials used in thermoforming are recyclable at the end of their functional life. To further reduce waste, many thermoforming manufacturers can collect excess materials from runs, granulate them, and integrate them with new resin to form new plastic sheets. This process reduces the amount of waste that the manufacturer sends to landfills.
6 Small or large products are possible with thermoforming
With the possibility to create sheets of varied sizes and countless different molds, thermoforming can create parts big or small. While other molding methods are typically inefficient with large products, the team at Global Thermoforming Inc. can confidently and accurately produce small or large parts. Our team has manufactured large parts like overhead airline storage bins, automotive door panels and center consoles, boating panels, and home siding panels.
7 Parts are high-quality and rival the performance of other manufacturing methods
Thermoformed products are built to last, where “good” isn’t good enough. Where metal parts rust and fiberglass is naturally brittle, thermoformed plastics are durable and high quality, without the risk of rusting. Depending on the application, materials can be chosen to achieve a specific effect. For boating panels and jet-ski panels, waterproof polymers are crucial to final product performance, while plastics like ABS can provide gloss characteristics.
Global Thermoforming Inc. is a leader in thermoforming plastics and has some of the tightest tolerances in the industry, with values as low as +/- .005”.
8 Tooling costs are lower
Because the pressure required for thermoforming is not very high, the tooling costs are lower than other manufacturing and molding methods. In addition, the lower requirement for tools and complex machinery reduces the upfront investment required for prototyping and product development.
9 Smaller volume runs are more cost-effective
Continuing from number 8 on this list, thermoforming is more cost-effective for smaller volume runs. This price difference is because of two intrinsic properties of the thermoforming process. First, the upfront investment is smaller because the tooling costs are lower than alternative solutions. Secondly, changing tooling and molding arrangements is incredibly flexible and easy with thermoforming, far faster than most other manufacturing methods. This flexibility reduces the time and labor required to make edits or change your design.
For large-scale runs, these differences in cost don’t matter as much because the wide profit margin of orders with such large volumes can absorb the difference. However, for runs of smaller volume, the reduction in upfront costs and time and labor required to tweak designs in the prototyping stage is essential to remaining cost-effective.
10 Lightweight products increase sustainability and efficiency
The lightweight plastic products created by thermoforming are often significantly lighter than metal or fiberglass alternatives. This weight reduction is particularly critical during transportation and shipping, where lower weight coincides with lower fuel consumption. As fuel consumption decreases, the client increases efficiency by spending less on fuel and decreases their environmental impact by reducing emissions related to fuel consumption.
Choose a Thermoforming Expert
Thermoforming technology is constantly evolving to provide the most efficient, rapid, cost-effective, and durable products. And with the numerous options available in terms of materials and molding methods, it’s crucial to collaborate with a leader in the space who can guide the entirety of the process.
Global Thermoforming Inc. offers a full range of concept development to production services related to thermoforming, with over 30 years of industry experience. With services ranging from design and prototyping to custom tooling, CNC trimming, measurement and quality control, and shipping, we have the skills necessary to provide a superior product and customer experience.
Reach out for a free quote today and begin your thermoforming journey.
Have an upcoming project?
Whatever your manufacturing needs may be, Global Thermoforming can put our engineering, design, and manufacturing expertise to work for you.