What Industries Benefit from Plastic Thermoforming?
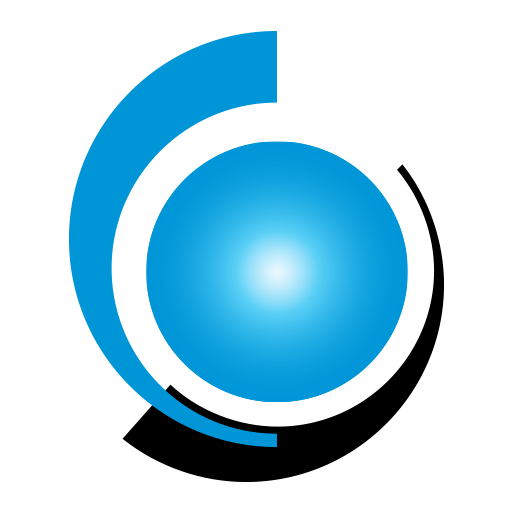
The advantages of plastic thermoforming techniques are driving market growth within a variety of industries. Thermoforming offers low tooling costs, fast product development and prototyping, and extensive design options. There are a wide range of thermoforming applications and virtually every industry can enjoy the many benefits, like cost-effectiveness and improved efficiencies, of thermoformed plastics.
Here is a list of some of the industries that benefit from thermoforming plastic:
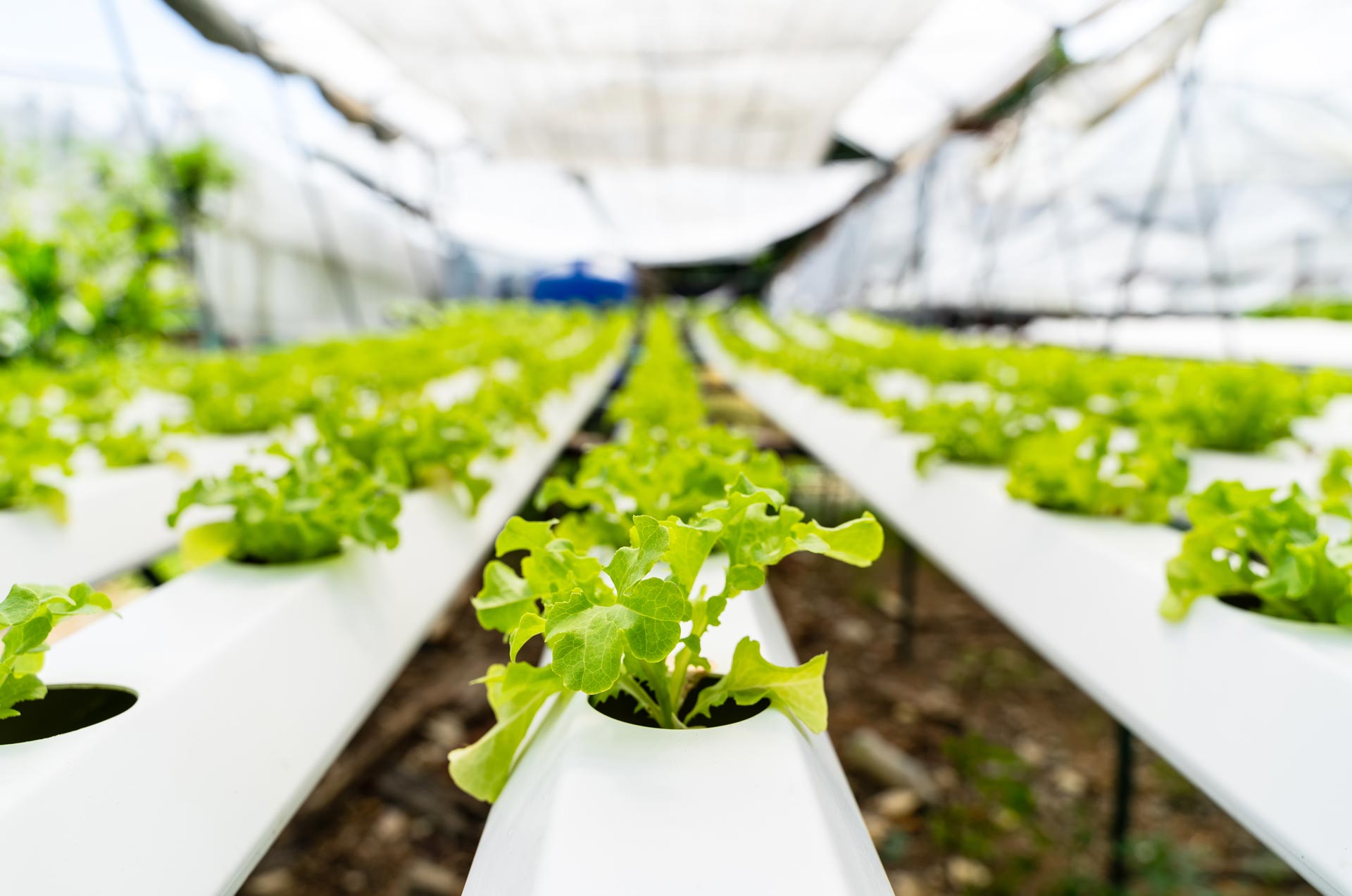
Aerospace Industry
The aerospace industry requires a variety of high-performance components crafted with precision. Durable, flame-resistant materials like Kydex, Royalite, and Boltaron are thermoformed to produce compliant, aerospace-grade products including:
- Overhead Storage Bins
- Cup Holders
- Arm Rests
- Ventilation Ducts
- Wall and Ceiling Panels
- Overhead Cabin Lights
Thick-gauge thermoforming creates industry-specific components with only the tightest tolerances (+/- 0.001” to 0.010”). Global Thermoforming has delivered error-free parts to clients like Raytheon and Collins Aerospace. The company builds its own tools and secondary fixtures while the in-house engineering team has access to on-site product development. These advantages ensure that clients receive their thermoformed plastics without delay. This process produces the best possible products at a fraction of the cost of previous methods.
Agriculture Industry
When seasonal changes demand operational pivots, plastic thermoforming with ABS plastics can accommodate a multitude of manufacturing needs in a timely and cost-effective manner.
Thermoformed plastics are well-suited for the following agricultural applications:
- Hydroponic Trays
- Plant Trays and Pots
- Tractor Fenders and Components
- Feed Bunks and Troughs
- Yard Equipment
Thick-gauge thermoforming is ideal for producing heavy-duty panels, roofs, and tractor interiors. This technique supports large-item creation while upholding all quality and safety standards. Vacuum-formed and pressure-formed products can be tailored to each client’s unique needs and ever-changing seasonal demands.
Appliances Industry
Today, nearly all refrigerators and freezers feature thermoformed liners. Plastic thermoforming is faster than other techniques making it a cost-effective alternative to injection molding. Thermoforming’s nuanced design capabilities can accommodate each appliance model’s unique specifications.
Inline thermoforming machines are ideal for appliance liner production. In fact, vacuum forming and plastic forming are two techniques that produce top-of-the-line parts, like refrigerator liners and appliance components with cavities. These methods work well for larger items while still maintaining the product’s quality and detailed design.
Global Thermoforming offers a great selection of high-performance materials. These thermoformed plastics last up to 50% longer than older generations and are used to make products like:
- Refrigerator Panels
- Microwave Components
- Oven Accessories
- Heating Panels
- Washing Machine Parts
Automotive Industry
Streamlining production revolutionized the auto industry and thermoforming industries are continuing this legacy. Thermoforming offers automotive manufacturers superior turnaround times and unparalleled quality.
Acrylic-capped ABS, TPO, Kydex, Royalite, and Boltaron are vacuum or pressure-formed to create the tightest possible tolerances (+/- 0.001” – 0.010”). Thick-gauge automotive thermoforming can produce the following components:
- Door Panels
- Exterior Components
- Instrument Panels
- Glove Boxes
- Consoles
Bath and Shower Furnishings Industry
Spa and bath manufacturers need crack-free custom products that are built to last. Thermoforming achieves cost-effective and durable custom designs for bathrooms, showers, spas, and more. Plastic thermoforming machines are equipped to process materials with up to 7’x11’x5 dimensions. This method can produce detailed designs for larger items with short lead times and fast turnarounds.
Thermoforming is used to create:
- Bathtub Shells
- Spa Tub Liners
- Shower Lining and Floors
- Soap Holders
- Shower Shelves
Consumer Products Industry
Everyone encounters thermoformed plastics on a daily basis. From food packaging to cosmetics and retail displays, these materials are a staple in the consumer goods industry.
Thin-gauge, inline thermoforming is used to produce a variety of consumer products and packaging. Some common consumer goods that use thermoforming are:
- Custom Packaging
- Food Containers
- Cosmetic Product Packaging
- Retail Displays
Thermoformed plastics are sturdy enough to withstand several handoffs yet user-friendly for consumers. With custom design capabilities, texture and color variety, and sustainable bioplastic options, every consumer brand can benefit from thermoforming techniques.
HVACs Industry
Thermoformed plastics play a critical role in supporting heating and cooling system performance. Thermoformed plastics can withstand sharp temperature changes, exterior weather conditions, and are durable enough to last for several years. HVAC thermoforming uses the vacuum-forming process to rapidly-produce quality products tailored to each client’s needs. These parts are manufactured to the tightest tolerances.
Thermoformed plastics are used to create the following HVAC products:
- Drip Trays and Pans
- Housings for Air Conditioning Units
- Portable Air Conditioning Panels
- Portable Space Heater Panels
Lawn and Garden Industry
Lawncare requires safe and durable equipment components. High-quality thermoformed plastics are durable and customizable, making these products ideal for lawnmowers, golf carts, and more. Thermoformed materials like ABS low gloss and ABS acrylics are commonly found on tractors, lawnmowers, and golf carts.
Thermoformed materials are long-lasting and low-maintenance making these products ideal to withstand the environmental demands that lawn care professionals face on a daily basis. Heavy-gauge thermoforming creates impact-resistant pieces that protect users and lawn care machines from debris and environmental conditions.
Examples of thermoformed lawn and garden components are:
- Interior Tractor Panels
- Fenders
- Riding Lawnmower Parts
- Pushmower Engine Covers
- Debris and Waste Enclosures
Marine Industry
Thermoforming creates durable products that meet the unique needs of an aquatic environment. UV-resistant, water-repellant plastics, like Kydex, are ideal for marine equipment manufacturing. Heavy-duty plastics, like ABS, support product integrity and safety for long-term use in aquatic and subsea environments.
High-quality materials and seamless production are crucial for marine equipment and thermoforming is an efficient technique that ensures sustained results.
Thermoformed plastics are used to manufacture the following products:
- Radomes/Radar Antenna Protectors
- Boat Panels and Components
- Jet Ski Panels and Components
- Yacht Panels
- GPS Covers
Medical Industry
High-quality functionality and aesthetics coupled with low tooling costs make thermoforming a top choice for medical equipment manufacturers. Thermoformed medical devices provide lower-cost tooling for large part production and faster lead times for high-demand medical products. Flame retardant ABS, PVC, and chemical-resistant HDPE and Kydex are used to create medical-grade, FDA-compliant packaging, and devices.
Thermoforming has lowered costs and supported faster production of much-needed medical supplies and equipment. Custom thermoformed packaging and equipment promote safety and efficiency that improves the healthcare employee and patient experience.
Medical products that use thermoformed plastics include:
- Reusable and Single-Use Face Masks
- Mobile Sanitizing Sinks
- Hospital Cabinets
- X-ray Equipment
Packaging Industry
Thin-gauge thermoforming produces quality plastic packaging for a variety of industries. Materials like PET protect valuable parts and components.
Thermoforming can be used to produce the following products:
- Electronic Components Packaging
- Automotive Trays and Components
- Medical Trays
- Semiconductor Trays
- Pop Displays and Clamshells
Durable thermoformed plastics can securely transport important parts and components. These cost-effective materials are used to protect items like USBs, computer chips, sterile medical supplies, and more.
Pool and Spa Industry
Precision and durability are crucial for pool and spa industry components. Only the highest-grade plastics and production methods can uphold the integrity of hot tubs, pools, and spa accessories through years of use. Vacuum-formed acrylics provide the durability and aesthetic appeal this industry requires.
Precision and customization for large items can be achieved with thermoforming techniques. Here are some pool and spa items that contain thermoformed plastic parts:
- Hot Tub Shells
- Packaging for Pool Parts
- Pools up to 11’ x 7’ x 5’
- Misting Machines
- Electrical Components for Pools and Hot Tubs
- Exterior Keypad Covers
Recreational Vehicles Industry
Thermoformed plastics provide the durability and aesthetic customization recreational vehicle interiors need. Thermoforming allows RV manufacturing clients to produce highly-detailed components in a shorter amount of time than other methods. This industry uses several types of thermoformed plastics to produce RV components including:
- ABS and Polycarbonate Alloys
- Polypropylene
- PPE
- SMA
Some recreational vehicle components produced with thermoforming include:
- RV Instrument Panels
- Interior Side Door Panels
- Dashboards
- Ceiling Panels
- Exterior Panels
Thermoforming helps recreational vehicle manufacturers produce sleek, reliable, and distinguishable components that elevate a brand’s aesthetic and performance.
Technology Industry
Global Thermoforming is an industry-leading thermoforming producer that helps technology companies revolutionize their respective industries. Thermoforming offers precision, reliability, and efficiency when critical industries need it most.
High-quality vacuum and pressure forming methods are used to create technologically-advanced thermoformed plastic components. Global Thermoforming’s vacuum forming process is built into stages so products with the tightest tolerances are manufactured with ease.
Thermoforming supports dynamic changes and rapid growth within the technology industry. Using 5-axis CNC routers and fire-resistant materials like Kydex, Royalite, and Boltaron products are swiftly shaped into durable designs for technology components.
There are many uses of thermoforming for technology applications. Here are a few ways thermoformed plastics are supporting the technology sector:
- Autonomous Vehicle Panels
- Military Drone Aircraft
- 5G Cell Phone Tower Covers
- Key Cutting and Fob Copying Machines
- Product Packaging
Windows and Siding Industry
Window and siding clients rely on the highest-quality materials to withstand the outdoor elements. There are several thick-gauge thermoformed plastics that perform well in harsh weather conditions. With thermoforming, UV-resistant and water-repellent materials are easily shaped into custom window and siding components.
Global Thermoforming works with leading companies across several industries. The company’s team of in-house engineers uses cutting-edge technology to design innovative solutions suited to each client’s goals. The Global Thermoforming team provides industry-specific guidance and design solutions to support innovation across industries.
Have an upcoming project?
Whatever your manufacturing needs may be, Global Thermoforming can put our engineering, design, and manufacturing expertise to work for you.