How Do Thermoforming Machines Work?
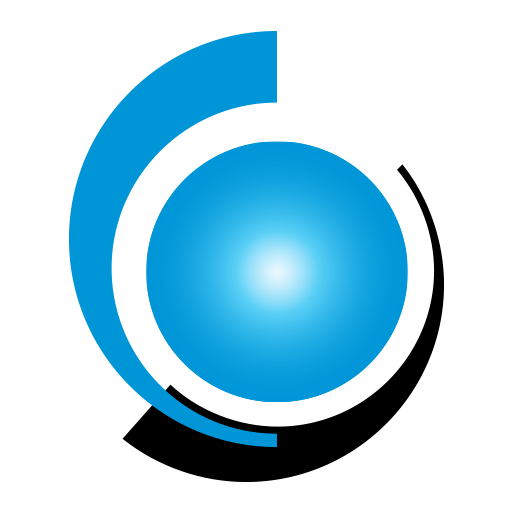
It’s a point of pride that our in-house capabilities at Global Thermoforming are diverse. We bring ideas to life with our thin and thick gauge material tolerances, dedication to quality, and commitment to excellence from the design to the final product. Our lineup of thermoforming machines makes our exceptional results possible and supports our mastery of producing a variety of products across many industries. Although our previous articles have talked about many aspects of the thermoforming process and materials – this month we’d like to share some insights into how our machines actually make the parts we produce.
How does a thermoforming machine work? Each of the machines in our manufacturing facilities works by heating thin plastic sheets and stretching them over a mold to create precise shapes. However, each approaches their task differently. We’ve talked about the general process of thermoforming in previous articles – so let’s see how our machines handle the work of creating all the aerospace, automotive, medical, food, and other industrial parts we produce.
Every component is created by heating thermoplastic, molding it into a 3-dimensional form, and finally trimming and finishing it into the final product. No matter the type of plastic, the size of the part, or the thickness, any part we produce at Global goes through one of three types of thermoforming machines: Rotary, Shuttle, or In-Line Roll-Fed. Let’s take a look at each and how they excel at their jobs!
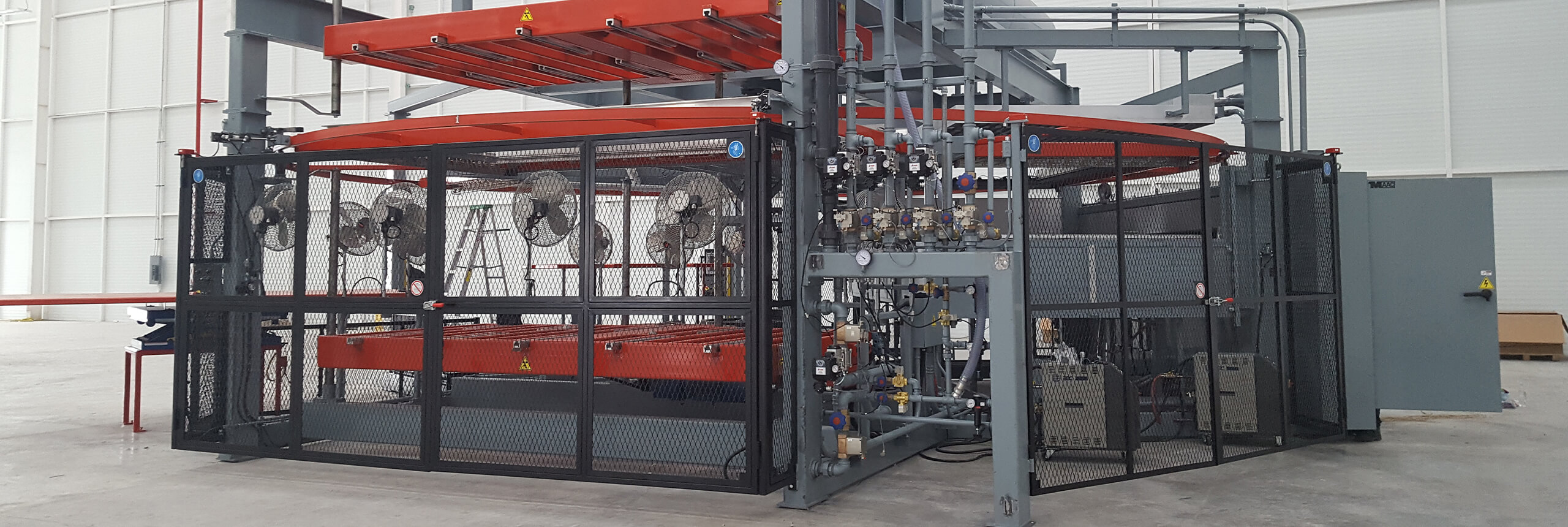
Rotary Thermoforming Machines
Rotary thermoforming equipment can increase productivity in forming operations by arranging three or four workstations around a central area. One important feature of this design: only one mold and one forming station are needed on a rotary machine.
As you would guess, a 3 or 4-station rotary unit is a configuration that creates an efficient, continuous workflow. Typically, there’s a load/unload station, a heating station, and a forming station. A four-station rotary adds a heating or cooling station. The rotary machines are fast and efficient. One sheet is always in the oven, and all stations are used simultaneously. With constant cycling, the temperature is consistent, and tolerances are tight.
Our MAAC Thermoformers are generally used to produce parts with an annual usage of over 1,000 units. These versatile machines, including our PP (Polypropylene) thermoforming machines, can utilize the vacuum, pressure, and twin sheet methods of forming as needed.
Shuttle Thermoforming Machines
Thermoformers such as our MAAC Comet machines are highly flexible parts of our manufacturing process. When you think of how plastic sheets move in and out of the thermoformer, that can be described by the term “shuttle”. These sheets of thermoplastic material are loaded manually into the clamp frames, which are then sent into the oven. Once the desired forming temperature is reached, the frames move over the mold, which rises to create a seal. Vacuum pressure is then used to form the part from the heated plastic.
Shuttle machines are real workhorses, as they heat and form the plastic in a single contained unit – using just one forming station and one heating area. They’re also highly adjustable and versatile. Our Comet C106S, for example, can handle parts up to 6′ x 10′. These machines not only move material quickly but also are superb at producing components for aerospace, medical, and automotive, and other industries.
Global uses MAAC, Shuman, and Brown shuttle thermoformers on our production floor, which allow us to utilize vacuum, pressure, and twin sheet forming processes as needed. Our focus on quality and consistency leads us to constantly seek out the best machines for our manufacturing facilities.
In-Line Roll-Fed Thermoforming Machines
This style of thermoforming machines is frequently used for thin-gauge items such as food trays, handling trays, clamshells, and blister trays. As with all our manufacturing, thermoplastics are the starting material of the process. In roll-fed machines, we use plastic roll stock material that can range in weight from 100-1,000 lbs per roll. The material is automatically and continuously fed into the machine, where it moves directly onwards through a 10’-12’ long oven.
After the material is heated to the correct temperature, it goes on to a forming station, then to a die-cutting station. We have machines that also feature a second die-cutting station and a stacking or robotic station. Because of these machines’ sheer speed, it’s beneficial to incorporate secondary operations within the unit. Global has both Sencorp & Brown units in our manufacturing facilities.
CNC Routers
Although our thermoforming machines are extremely versatile, our thick-gauge components typically go on to a 3-axis or 5-axis CNC router for additional finishing after they’re formed. Global can also handle the removal of excess plastic and perform any other operations that require holes, cutouts, or other design features.
Our Thermwood and DMS router models utilize Computer Numerical Control for tight and consistent tolerances. Using digitized data, a computer and CAM program control, automate, and monitor the router’s precise movements. The CNC controller works with a series of motors and drive components to move and direct the machine axes, executing the programmed motions.
At Global Thermoforming, we’re experts in matching the right machine to your needs. Our team is ready to get your products onto the market in the most efficient way – by matching the right designs, materials, mode of forming, and finishing to your specifications. We welcome your questions about assisting your business with our engineering, design, and manufacturing expertise.
Have an upcoming project?
Whatever your manufacturing needs may be, Global Thermoforming can put our engineering, design, and manufacturing expertise to work for you.