Quality Thermoforming Explained in 5 Minutes
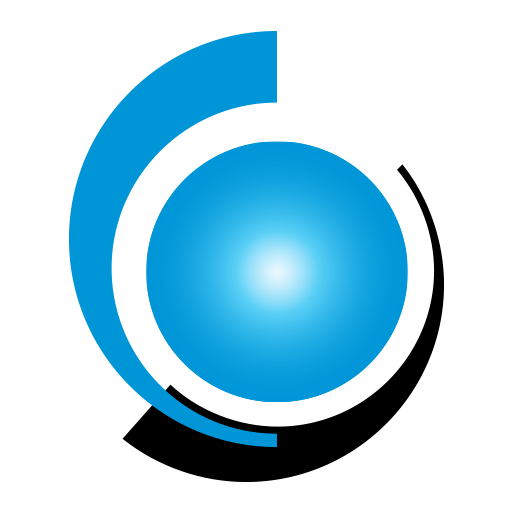
Everyday consumer products from ice cream tubs to sterile packaging are created through the process of thermoforming. This manufacturing process happens when large plastic sheets are heated to a specific temperature until they are easily molded into the desired shape. People use products designed and formed by a quality thermoforming process without even realizing it.
So, what is the difference between everyday thermoforming and quality thermoforming? Global Thermoforming is at the epicenter of quality thermoforming, so let’s explore the various components.
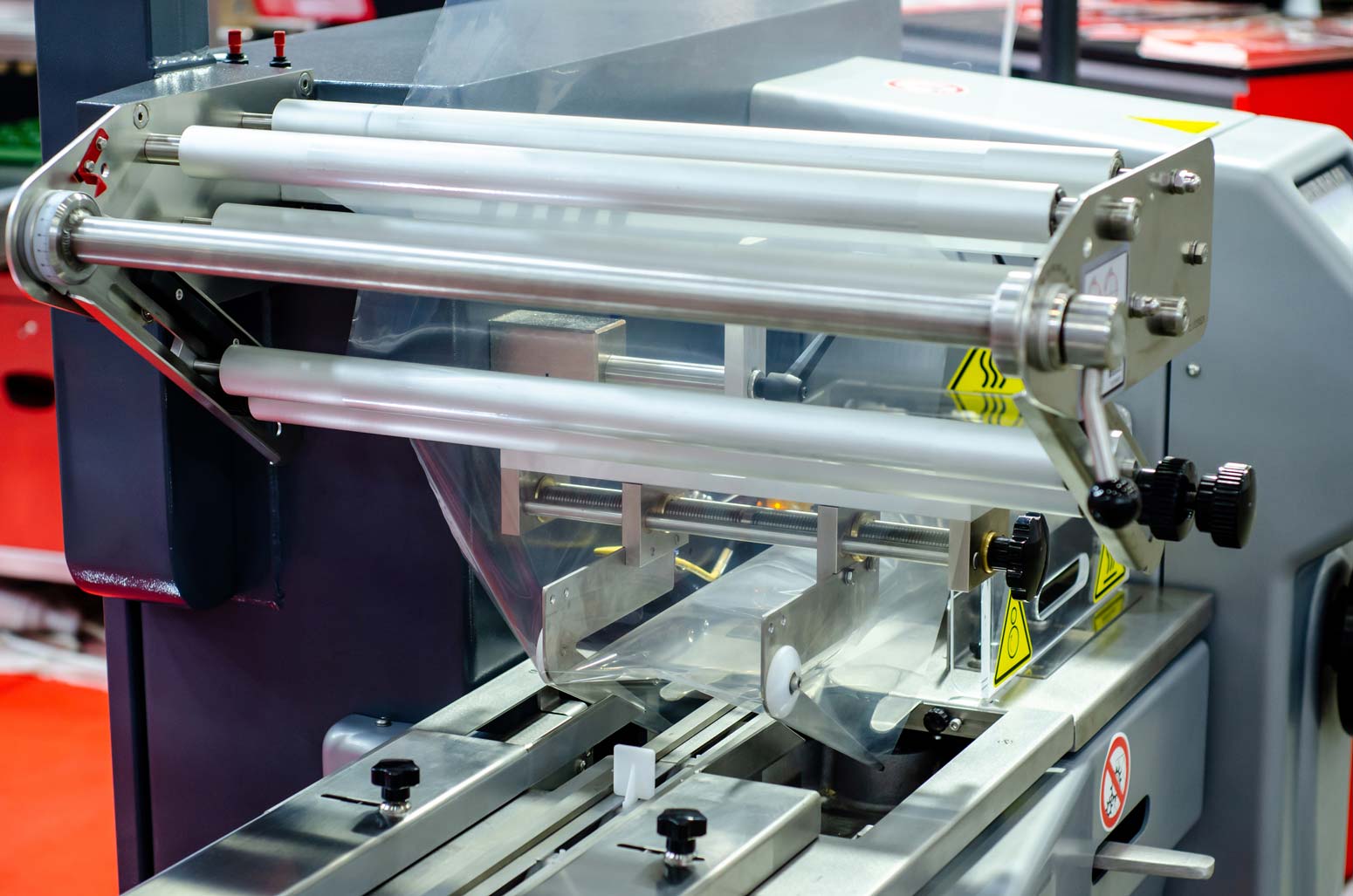
What is Quality Thermoforming?
Quality thermoforming is achieved when following an exact step-by-step process. If the temperature is incorrect or the trimming process is misjudged, there can be a lot of waste produced in the process. Global Thermoforming values its environmentally friendly operations and aims to create minimal waste. We also recycle 100% of our materials so that plastic is never discarded without being put to use.
In addition to putting the environment first, Global Thermoforming goes above and beyond to ensure quality is the priority of our business. We take extra measures to assure quality control is in place, so that customer satisfaction is always at the highest level possible. There are many specific measures in place to ensure quality thermoforming is achieved. Global has set the standard for what it takes to be considered a quality thermoforming company as an industry leader in plastics manufacturing. Below are just a few steps we take to ensure the best possible quality.
How Does Global Thermoforming Ensure The Highest Quality?
Why The ISO Certification Matters
An ISO certification or ISO standard may look familiar to many consumers, but it is rigorously standardized by a non-governmental organization based in Switzerland. The process to become compliant with these standards was extensive and helped us understand how important every detail of thermoforming was for each of our projects. With these standards in place, product safety and quality are at the forefront, yet there is still room for innovation in an ever-growing industry.
The ISO certification shows that numerous procedures, protocols, and reviews have been implemented to ensure compliance. More specifically, Global undertook a series of eighteen steps to achieve its ISO 9001:2015 certification. This serves as a framework for enhancing the quality and providing consistently on-target products for our customers. The certificate also helps us improve our overall efficiency, which allows us to achieve business goals and meet customer satisfaction rates.
Global's ISO 9001:2015 Checks and Balances
One of the essential elements of the ISO certification is the commitment to a Plan-Do-Check-Act cycle. This is a standardized way of ensuring that the company is always committed to improving and examining how we can meet our customers’ needs more effectively. As a result, Global Thermoforming continually evaluates how we can improve our processes to benefit our customers, from risk-based thinking to leadership participation.
Quality Management Systems are also acknowledged in the ISO certification. Global’s best possible practices are permanently adhered to, especially since we are responsible for creating medical, automotive, and aerospace products. Global is always held to the highest standard with a list of seven essential quality tools, creating a premium customer experience that surpasses every project we complete.
The Impact of the ISO Certification on Customers
Global Thermoforming is fully transparent when explaining how our ISO certification impacts our customers’ projects. So whether they’re wondering what the best manufacturing process is or require the highest quality final product, it’s easy to make an informed decision after a discussion with Global Thermoforming.
Global Thermoforming is committed to finding solutions for its customers, even when problems arise. As a result, we can always guarantee customer satisfaction, especially with our series of procedures in place with the ISO 9001:2015 certification.
Staff Training for a Quality Thermoforming Process
Enhancing Quality Control as a Thermoforming Company
Global Thermoforming is committed to continuing to take measures to reinvest in new enhancements to the company. Enhancing processes, streamlining inefficiencies, and increasing production time without compromising quality are achieved when our team is given the time to learn and improve their knowledge.
Global may enhance quality overall through 3D printing, which will help create faster prototypes. It is now possible to use over 30 materials to 3D print, which speeds up the process considerably. Cutting the lead time for a tool from three to five weeks down to one week is a massive advantage for those who work with us.
Ensuring the highest possible quality is not our only key differentiator; Global Thermoforming is also committed to being an energy-efficient thermoforming company. Updating our solar panels on the rooftop of our plant in Tempe, AZ, will help to reduce our carbon footprint.
What Are The Steps Of Thermoforming?
The first thermoforming stage begins with a TUFFAK polycarbonate sheet, which will eventually be molded into the final plastic product. Reaching 250 degrees Fahrenheit is the goal because lower temperatures will require a longer time frame to dry the sheet effectively.
Once this stage of pre-drying is completed, the thermoforming process can begin. There are many techniques, but the basic process remains the same. The sheet is placed into the clamping frame with both top and bottom heater banks to heat the sheet. As soon as the correct temperature is achieved, the desired shape can be created, and the final product will begin to look as it should. Once this step is completed, it has to cool and trim to produce the highest quality final product.
Less Experienced Thermoforming Companies: Where They Could Get It Wrong
Not all thermoforming companies will be well versed with quality control processes like Global Thermoforming. For example, it’s highly recommended that new customers order prototypes first because things are bound to change. If there are any problems, they can be ironed out at the prototype stage before the manufacturing process begins. This saves a lot of time and money for both the company and the customer.
When customers expect a process to be completed without going through the appropriate quality control steps, they rush the intricate process. Cutting corners is never a good thing, which is why Global has its ISO certification in place. Unfortunately, many companies don’t double and triple-check every part of the process as thoroughly as Global Thermoforming.
Global Thermoforming's Future Plans
Global Thermoforming’s big plans revolve around creating more quality products as we grow and expand in the plastic manufacturing industry. There is a lot of competition for thermoforming, which can cause many companies to fall short when it comes to quality. This is something that Global will never compromise on, especially now that we have the ISO certification and well-versed procedures in place.
The highly competitive thermoforming and plastic manufacturing industry is an industry that presents a plethora of possibilities and opportunities. However, it also requires buckets full of passion, dedication, vision, flexibility, and a clear focus on delivering what the customer wants. Global will always keep a close eye on the industry’s market trends and emerging patterns to bring all of these possibilities to light. As much as innovation and speed are paramount if you want to be a frontrunner, quality will always be the primary mission for Global Thermoforming.
Making a name for yourself in the world of thermoformed plastics is possible. Still, a bad reputation can quickly be obtained if the processes and procedures do not consistently meet customers’ standards.
Delivering cutting-edge products that are innovative and ahead of the curve compared to other industry leaders will remain a goal for Global Thermoforming. In addition, making the most of the latest technology and adhering to quality control practices will undoubtedly be a part of our company’s future. All in all, Global Thermoforming is always clear about its focus on innovation and customer experience, as well as our unwavering understanding of industry standards and quality control assurance for each product we create.
Have an upcoming project?
Whatever your manufacturing needs may be, Global Thermoforming can put our engineering, design, and manufacturing expertise to work for you.