Difference Between Thin-gauge Thermoforming vs Thick-gauge Thermoforming
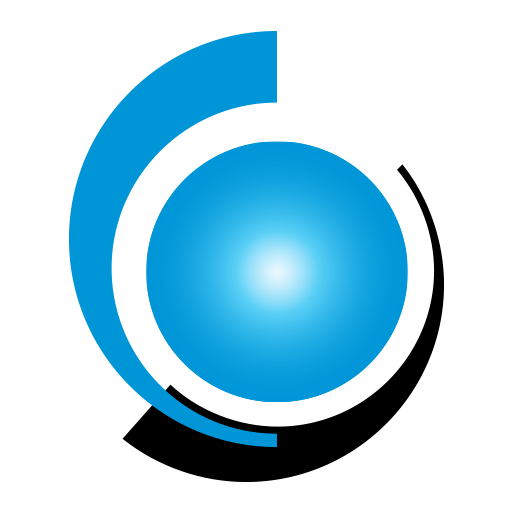
Global Thermoforming is a leader in providing a broad array of thermoforming and plastic manufacturing capabilities. As such, you’ll see a lot of references to both thin-gauge thermoforming vs thick-gauge thermoforming on our site. In this blog, we point out the differences between the two types, discuss their applications, and touch on some of the machines and processes that we’ve discussed in earlier articles. We know we’re biased, but learning about how vital plastic thermoforming is to daily life is pretty eye-opening!
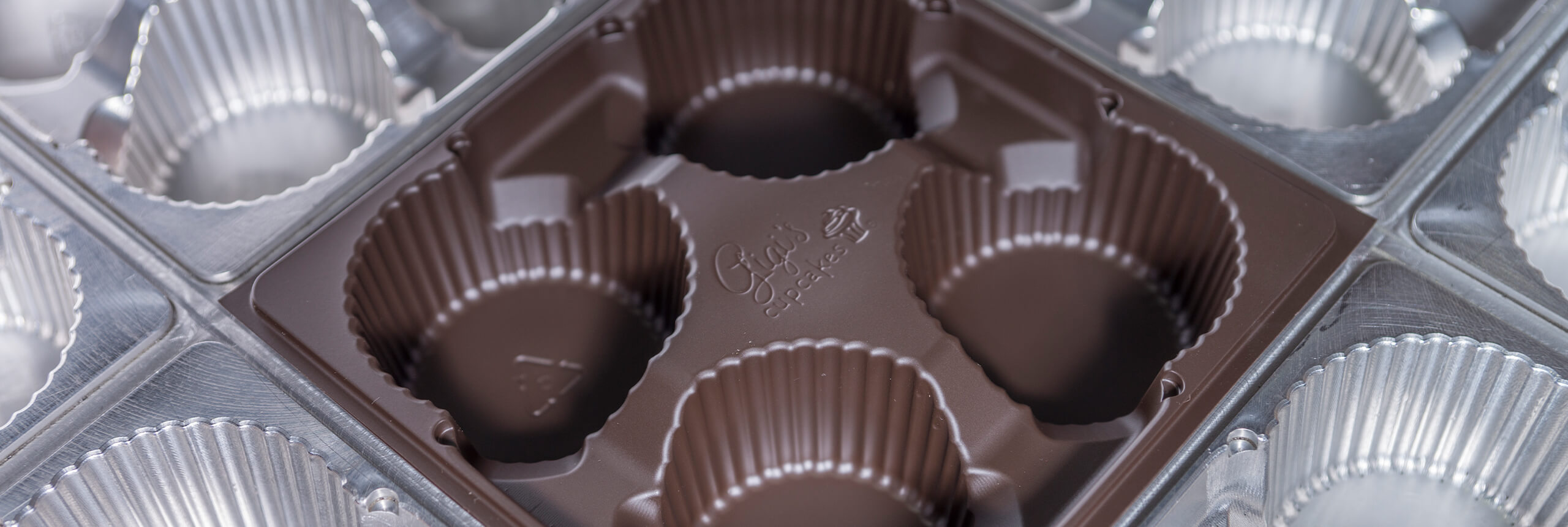
Thin-Gauge Thermoforming vs Thick-Gauge Thermoforming
Thin-Gauge Thermoforming
We’ll start with thin-gauge thermoforming, which are used in making products that are familiar to all of us. If we’re looking at manufacturing specifications, thin-gauge plastics are usually under .06” thick, and flexible. In most cases, thin plastics are intended to be disposable and recyclable and are a valuable part of modern daily life. Some examples of thin-gauge plastics are protective plastics of cosmetics packaging, candy trays, and clamshell packaging.
Our Sencorp 2500 Inline Forming machine has the impressive ability to produce thin-gauged items such as packaging in runs of 3-10 second cycles, versus a single station or shuttle machine which usually ranges from 3-10 minutes per cycle. When you multiply that by your overall product order quantity, using a machine like ours can drastically improve the overall production timeline, meaning you receive your order much more quickly.
The production of these items is quick, can be carried out in large quantities, and with our high-quality molds, they’re extremely customizable. As a manufacturing facility that takes products from design to production, we’re continually working with new ideas and applications for thin-gauge plastic components to provide better value for our customers.
Some of the enhancements we’re able to offer with our thin-gauge thermoforming include finely detailed molds. This technique assures the execution of tiny details on both curved and flat surfaces is clean and precise. As seen in the example of thin-gauge packaging design, the combination of thinner plastic and the precision of the pressure forming creates impressive results. Even transparent plastics can display logos and textures that are crisp and clean – ready to promote your business and package your products. Integrating these functional and aesthetic details with precise, error-free results is part of what we do at Global Thermoforming. Our stringent quality controls are a core value.
Though utilized for different purposes, thin-gauge thermoforming involves the same general thermoforming processes as thick-gauge thermoforming. After designing the mold, roll-fed sheets of plastic are heated and placed over the mold using a press or vacuum. The hot (thermo) malleable sheets then conform (form) to the mold, producing a precisely made thermoformed product.
For a glimpse at one of the machines we use for this step, check out our Sencorp 2500 Inline Thermoforming Machine.
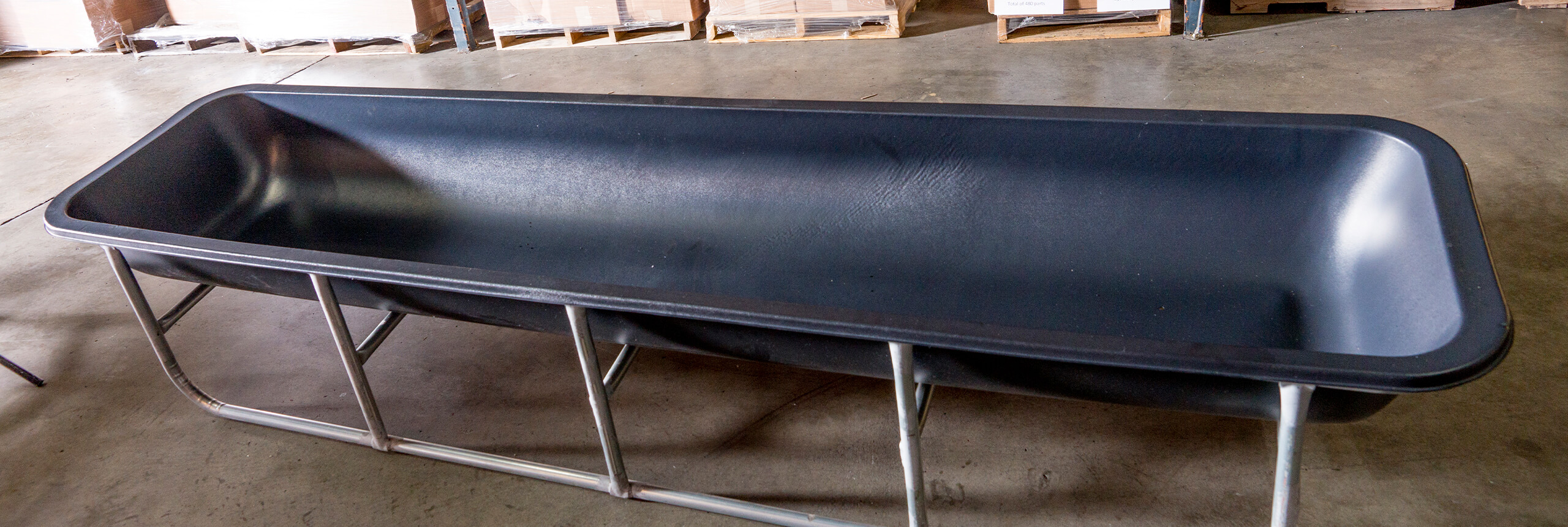
Thick-Gauge Thermoforming
The process of thick-gauge thermoforming is most useful when longer-lasting, sturdier components are needed. In thick-gauge thermoforming, the thickness enhances the overall durability of each piece. Lower tooling costs and shorter set-up times compared to injection molding are a significant advantage to this process. Injection molding commonly uses more complex, intricate, and double-sided molds that liquid plastic is injected into. The process of tooling these molds can involve much longer engineering and design times before production begins. Other advantages show up in the final product, with thermoformed plastic providing larger parts that look great without painting. Please refer to our previous blog for further information on the differences between thermoforming and injection molding.
We’re describing the advantages of thin and thick-gauge thermoforming in this article and should mention that we have the ability to accomplish amazing, one-of-a-kind results by adapting traditional injection molding designs into thermoforming. This approach can sometimes be the most efficient way to approach challenging projects, with the benefit of at least a 4-5x decrease in tooling costs. Since we recognize our clients have specific needs, our team has designated a portion of our manufacturing facilities for manufacturing these specialty designs.
The nearly limitless customizability of thermoformed plastics has made them essential to almost every industry. It’s part of our daily lives and safe activities. Global Thermoforming has capabilities for parts up to 1” thick at our facilities. Some great examples of thick-gauge thermoformed products that you interact with regularly are dashboards and other car interior parts, as well as mass-transit surfaces.
The resilient, more substantial plastics utilized in thick-gauge thermoforming, such as polycarbonate, ABS, HDPE, HMWPE, Kydex and Royalite are used in innumerable ways to benefit the public: airport luggage totes, enclosures for medical equipment such as MRI, x-ray, and CAT scan machines; fitness equipment, and many home appliances. Once you’re aware of how versatile thermoforming is, you’ll begin seeing it used everywhere!
Thick-gauge thermoformed parts are more rigid and can be shaped, drilled, routed, and cut after they’ve gone through the standard thermoforming process we talked about above. Using machines like our new DMS 5-Axis CNC router, Global Thermoforming produces parts, components, and products with industry-leading precision and speed.
Quality Thermoforming
Thin-guage thermoforming vs thick-gauge thermoforming; which is better? With both thick and thin-gauge thermoforming, our expertise has allowed us to exceed expectations and deliver the highest quality in the industry for over 35 years. Our experience with close tolerance forming and our trimming capabilities covers the full range of thermoplastic materials. If you have any questions about the best type of plastics, most efficient or economical processes, or possible uses for any product, we invite you to get in touch.
At Global Thermoforming, we stay involved through the entire process, and our ability to produce large parts with thin walls in a variety of shapes has led to the use of thermoforming in many diverse industries we serve. Including Aerospace Components, Medical Components, Bath & Shower Furnishings, Pools & Spas, Recreational, Vehicle Components, Sidings & Windows, Consumer Products, Appliances and Housewares, Automotive Components, Marine Components, Lawn & Garden, Agricultural Components, HVAC Components, Disposable Packaging. Contact us to learn more about Global Thermoforming.
Have an upcoming project?
Whatever your manufacturing needs may be, Global Thermoforming can put our engineering, design, and manufacturing expertise to work for you.