Top 10 Things You Didn’t Know About Thermoforming
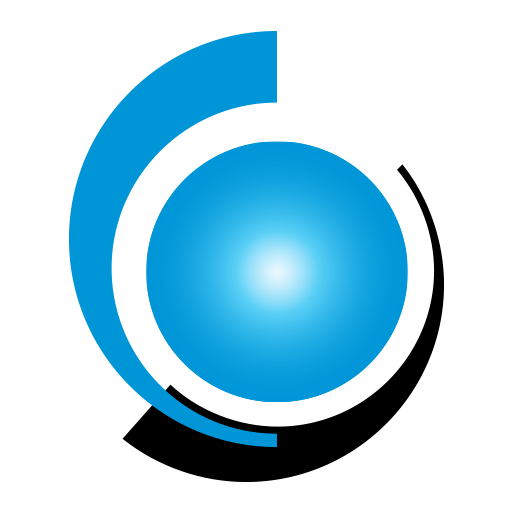
Thermoplastics date back to the mid-1800s, when they were first used as a substitute for ivory. Today, these materials play a crucial role in many manufacturing operations. From medical devices to household appliances and food packaging, thermoformed plastics have become a part of modern daily life.
Thermoforming is an innovative plastic manufacturing technique in which thermoplastic sheets are heated to a softening point. The sheets are stretched across a mold and allowed to cool and harden into the desired shape. Thermoforming creates high-quality, custom products at a fraction of the cost of other plastic forming methods.
Product design flexibility, cost-effective production, and automation are just a few of this method’s many benefits. In fact, virtually any industry can see positive results with thermoforming’s versatile production capabilities and a wide variety of applications. Here are the top 10 things you didn’t know about thermoforming:
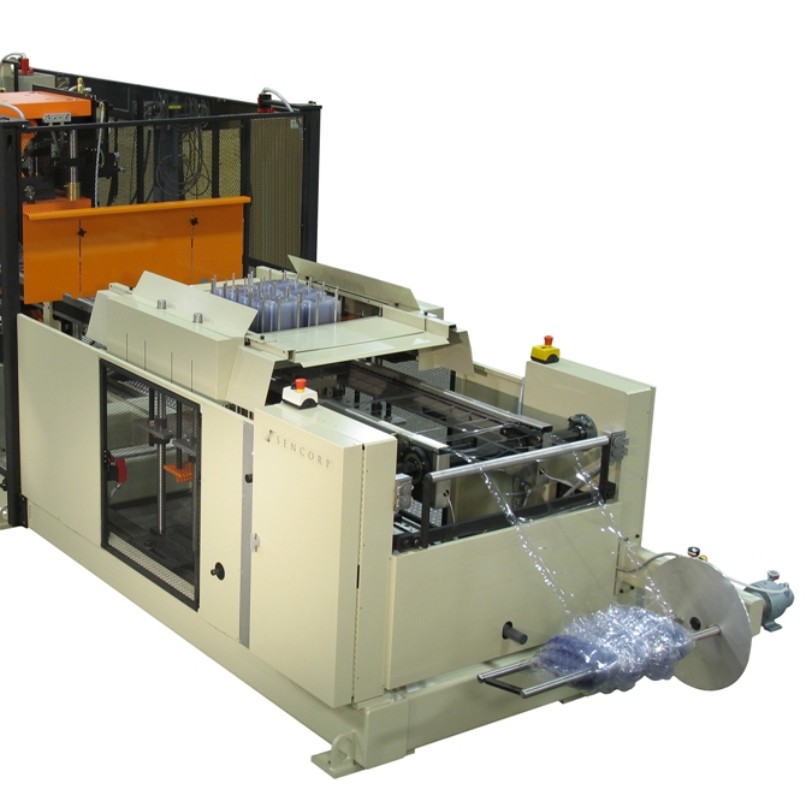
1 There Are Different Thermoforming Methods
While vacuum forming is the most common technique, there are three main types of thermoforming. The chosen method is determined by the shape, size, and material used for product development. Thermoforming manufacturers determine which method is best for each client’s needs.
- Vacuum-Forming Method: Vacuum forming is a fairly simple type of thermoforming because this method only uses one mold at a time. The part is formed by using a vacuum to heat and stretch plastic over a mold. This method is typically employed for shallow plastic parts that require cavities. Vacuum-formed plastics are a viable alternative to fabricated sheet metals, fiberglass, and injection-molded materials.
- Pressure-Forming Method: With this method, pressure is applied to the backside of the mold as plastic sheets are pressed and heated to achieve the desired shape. The pressure-forming method enables corners to have smaller radii, which gives parts a sharper appearance. This technique is ideal for tight tolerances and produces consistently molded features.
Twin-Sheet Method: Two molds and two plastic sheets are pressure-welded together to create the desired product shape. This method is ideal for quickly producing strong doors, panels, dual-sided flooring, and containers.
2 Thermoforming Works for a Variety of Materials
Thermoforming offers great versatility for product design and works well with several materials. The material used for a thermoforming project will be determined by the product’s intended use and additional industry-specific regulatory considerations. Here are some commonly-used thermoformed materials:
- Acrylonitrile Butadiene Styrene (ABS): This material is commonly used for thermoforming due to its versatility and sturdiness. ABS is available in a large variety of colors and textures. This material is a great choice for automotive components, covers, and seating.
- Acrylic: This material is transparent and impact-resistiant. It is a sturdy alternative to glass which is why it is used to produce windshields, signs, aquariums, and TV screens.
- High-Density Polyethylene (HDPE): This material is resistant to chemicals and impact. HDPE performs well in cold temperatures too. This lightweight, non-toxic material is used to create battery trays and storage bins.
- High-Impact Polystyrene (HIPS): HIPS is a low-cost material and brittle, yet forms easily. HIPS offers good impact resistance and dimensional stability, so it is ideal for creating parts for prototypes, covers, and containers.
- Polyethylene Terephthalate (PET): PET is commonly used for food packaging and can be FDA certified. PET is clear, lightweight, and recyclable.
- Polyethylene Terephthalate Glycol-Modified (PETG): A variation of PET, this material is molded into blister packaging and trays.
- Polyvinyl Chloride (PVC): Flame-retardant PVC is corrosion and chemical resistant and performs well in extreme weather conditions. Due to these durable characteristics, this material is frequently used for drain pans, housing, and packaging.
Thermoplastic Polyolefin (TPO): TPO is known for its high-impact-resistant properties. This durable material is also resistant to cold weather conditions and chemicals. TPO is commonly used for paint masking and exterior automobile components.
3 Thermoforming Has Many Uses and Applications
Thermoforming promotes greater efficiency and versatility, making it a cost-effective option for businesses of all sizes. These are just a few of the industries that benefit from thermoformed products:
- Aerospace: Thermoforming is used to develop overhead luggage bins, interior aircraft paneling, seats, window shades, and galley components.
- Automotive: Dashboards, air ducts, seats, and bumpers are comprised of thermoformed plastic components.
- Construction: Thermoforming is used to create skylights, toolkits, and machine covers.
- Fitness: Gym equipment, like treadmills, and sporting goods use thermoformed plastics to produce products.
- Office Supplies: Electronics packaging, office chairs, printer enclosures, and panels contain thermoformed plastic parts.
- Medical Equipment: X-Ray, CT, and MRI enclosures, sterile packaging, and medical device trays are made from thermoformed components.
- Transportation: Bus seats and panels, dashboards and exterior transportation parts often have thermoformed plastic parts.
From ice cream cartons to household appliances, vehicles to medical devices and equipment, thermoforming techniques are used to produce commonly-used items and tools.
4 Thermoformed Plastics Offer Sustainable Options
Modern consumers care about sustainability. Bioplastics offer a cost-effective way to deliver eco-friendly products and packaging to a company’s clientele. As an ever-evolving industry, thermoforming companies are developing eco-friendly plastic alternatives, and customers are willing to pay more for these greener packaging options.
5 Thermoforming is Faster Than Injection Molding
Injection molding fills liquid plastic polymers into a mold using high temperatures and pressure. Once cooled, the hardened plastic parts are released from the mold. This technique uses harder materials, like steel.
Thermoforming is a faster, and often cheaper, alternative to injection molding because thermoplastic sheets are used to shape the object over a mold’s surface. Thermoforming is more efficient due to the speed at which thermoforming molds can be produced. This process allows for faster product development and prototype testing.
6 Thermoforming Has Shorter Lead Times
Thermoforming offers lead times of 8-14 weeks from start to finish. With this method, tooling typically takes 3-8 weeks and production can be completed in 2-6 weeks. The injection molding process takes a substantially longer amount of time, usually 24 weeks, to complete production.
Automation and artificial intelligence allow thermoforming industries to harness the power of modern technology. Increased mechanization and production speed give companies greater creative liberty and better troubleshooting abilities to deliver a strong competitive advantage.
7 The Benefits of Low Tooling Costs
Plastic-formed products give companies affordable alternatives to steel and fuel-driven product production. The main cost of thermoforming is the creation of the mold. Thermoformed molds are much less expensive than other methods, like injection molding and sheet fabrication.
The upfront cost of thermoforming is often substantially less expensive than the injection molding technique. Tooling costs are lower for thermoforming due to the relatively low level of forming pressure used in this process. Plastics do not rust or fade like other materials, making thermoformed materials an appealing and cost-effective alternative to fiberglass or steel products.
8 Heavy-Gauge and Thin-Gauge Options
A material’s thickness is an important consideration for thermoforming. The dimensions of plastic sheets dictate whether thin-gauge or heavy-gauge thermoforming is used. A plastic sheet that is less than .06 inches thick is considered a thin gauge. Heavy gauge refers to materials with a thickness between .06 inches and .5 inches.
Thin-Gauge Thermoforming is ideal for making plastic cups or food packaging and commonly uses PETG, PET, and PVC to produce items. Thin-gauge thermoformed products are part of daily life, like small medical supplies, single-use packaging, and disposable plates.
Heavy-Gauge Thermoforming is used to produce sturdier, often larger items. Materials like ABS, HDPE, and HIPS are used to produce luggage components, home appliance pieces, and storage or shipping containers.
9 Thermoforming Offers Flexible Product Design
This plastic-forming process offers greater design flexibility because it requires lower forming pressure. With this method, a small number of prototypical parts can be produced in a short amount of time. Therefore, high-quality, custom products can be created swiftly and efficiently.
Thermoforming machines yield fewer knit, or weld lines, than injection molding. Small wall thickness allows designs to fill small spaces, generating greater detail and precision.
10 Thermoforming Produces High-Quality, Reliable Products
Thermoforming holds many advantages over traditional forms of plastic molding. Thermoforming techniques improve efficiencies and cost-effectiveness because many parts can be created from the same material.
Any design or fit issues can be assessed early in the production process to avoid costly delays and ensure optimal results. The thermoforming process promotes safety with tamper-proof packaging options. This method produces lightweight yet sturdy parts that preserve product integrity for a fraction of the cost of alternative techniques.
Forming Innovative Solutions for Modern Problems
What you didn’t know about thermoforming is that technological advancements are revolutionizing thermoforming industries and creating new market opportunities. Global Thermoforming is an industry-leading thermoplastics producer that offers full-range concept development and production services for small-run and high-volume projects.
Global Thermoforming improves client efficiencies by offering a wide array of plastic manufacturing capabilities. From part design to post-production machining, tooling manufacturing to thermoformed packaging, the company works tirelessly to ensure client success.
Global Thermoforming is committed to customer service. With a nuanced understanding of the thermoforming industry and a relentless pursuit of innovation, the company offers unique solutions for each customer’s needs and works tirelessly to achieve each client’s production goals.
Have an upcoming project?
Whatever your manufacturing needs may be, Global Thermoforming can put our engineering, design, and manufacturing expertise to work for you.